Welding additive trailing ultrasonic impact device and operation method
An ultrasonic impact and follow-welding technology, applied in the field of 3D printing, can solve the problems of difficulty in ensuring that the follow-weld impact point is located in the high-temperature plastic zone of welding, without considering the adjustment of the follow-weld impact lag time, and increasing the moving load of welding additive equipment. Easy operation and intelligent control, stable ultrasonic impact treatment process, high ultrasonic transmission efficiency
- Summary
- Abstract
- Description
- Claims
- Application Information
AI Technical Summary
Problems solved by technology
Method used
Image
Examples
Embodiment Construction
[0047] Below the present invention is further described:
[0048] see Figure 1-7 ,
[0049] The invention discloses an ultrasonic impact device for welding additive materials with welding. The device description: the connecting sleeve 208 is connected with the 3D moving column 406 of the gantry welding machine, the ultrasonic vibrator 300 is floating on the connecting sleeve assembly 200, and the front end of the ultrasonic vibrator horn 302 Ultrasonic impact treatment of the welding layer by the steel ball 301 reduces the friction of the ultrasonic vibrator moving with the welding and avoids the deflection of the ultrasonic vibrator; the upper part of the connecting sleeve is equipped with a pre-tightening ring 210 and an elastic ring 209 for adjusting the pre-pressure of the ultrasonic impact; The thickness of the welding layer or weld seam changes, the load of the ultrasonic vibrator is stabilized, and the resonant frequency is stabilized. The lower part of the connectio...
PUM
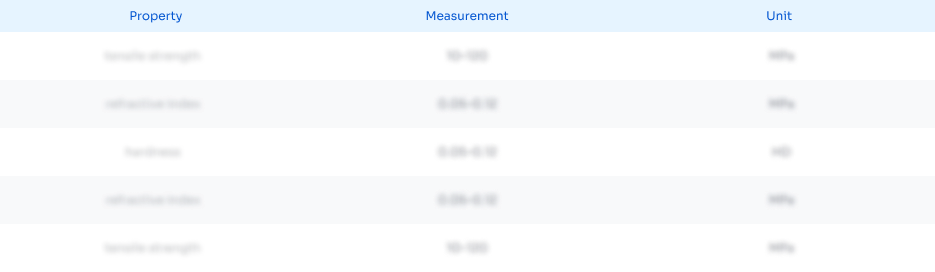
Abstract
Description
Claims
Application Information

- R&D Engineer
- R&D Manager
- IP Professional
- Industry Leading Data Capabilities
- Powerful AI technology
- Patent DNA Extraction
Browse by: Latest US Patents, China's latest patents, Technical Efficacy Thesaurus, Application Domain, Technology Topic, Popular Technical Reports.
© 2024 PatSnap. All rights reserved.Legal|Privacy policy|Modern Slavery Act Transparency Statement|Sitemap|About US| Contact US: help@patsnap.com