Silicon carbide fiber heat treatment roller bed furnace
A silicon carbide fiber, roller furnace technology, applied in furnaces, furnace types, lighting and heating equipment, etc., can solve the problems of dust generation, uneven temperature, time-consuming work, etc., to save energy and improve production efficiency.
- Summary
- Abstract
- Description
- Claims
- Application Information
AI Technical Summary
Problems solved by technology
Method used
Image
Examples
Embodiment Construction
[0030] The present invention will be described in further detail below in conjunction with the accompanying drawings and specific embodiments.
[0031] Figure 1 to Figure 12An embodiment of the roller furnace for heat treatment of silicon carbide fibers of the present invention is shown. The roller furnace for heat treatment of silicon carbide fibers in this embodiment includes a conveying roller table 50 and a feeding roller table 100 arranged at one end of the conveying roller table 50 , and the blanking roller table 200 located at the other end of the conveying roller table 50, the conveying roller table 50 is sequentially provided with a first cleaning transition chamber 501, a non-melting section furnace body 504, and a second cleaning transition chamber from the feeding end to the feeding end. The warehouse 503 , the furnace body 502 of the thermal crosslinking section, and the third cleaning transition warehouse 505 , the first cleaning transition warehouse 501 , the s...
PUM
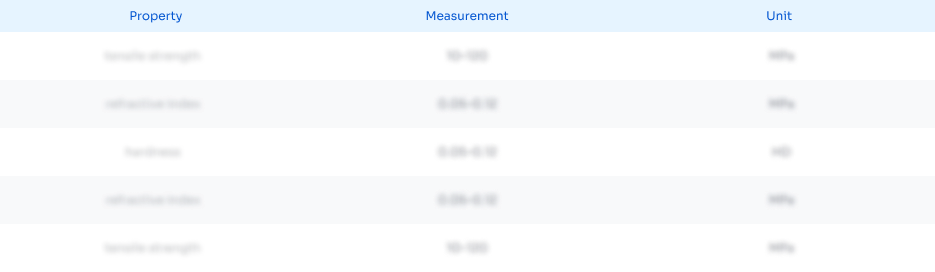
Abstract
Description
Claims
Application Information

- R&D Engineer
- R&D Manager
- IP Professional
- Industry Leading Data Capabilities
- Powerful AI technology
- Patent DNA Extraction
Browse by: Latest US Patents, China's latest patents, Technical Efficacy Thesaurus, Application Domain, Technology Topic, Popular Technical Reports.
© 2024 PatSnap. All rights reserved.Legal|Privacy policy|Modern Slavery Act Transparency Statement|Sitemap|About US| Contact US: help@patsnap.com