Method for pelletizing and vanadium extracting from vanadium extraction tailings
A technology for extracting vanadium tailings and making pellets, which is applied in the field of vanadium metallurgy, can solve problems such as low vanadium extraction rate, lower roasting conversion rate, and deterioration of equipment working conditions, and achieve the effect of stable and controllable roasting equipment and reduced roasting time
- Summary
- Abstract
- Description
- Claims
- Application Information
AI Technical Summary
Problems solved by technology
Method used
Examples
Embodiment 1
[0043] Take 1kg of sodiumized roasting water leaching vanadium tailings, the vanadium content is 0.92%, and the vanadium-titanium magnetite particle size is 81.03% 0.2kg through a 120 mesh sieve, and the two are evenly mixed and dried until the moisture content is 4.86%. Mixture 1 is obtained; mixture 1 and sodium carbonate are mixed according to the mass ratio of sodium and vanadium elements of 1.4 to obtain mixture 2; the bonding solution is carried out according to the mass ratio of sodium hydroxide, humic acid and water of 0.1:1.0:18.0 According to the preparation of wet pellets with a water content of 15-20%, the bonding solution is mixed with the mixture 2 and the wet pellets are pressed to control the particle size of the wet pellets to 25-30mm, and the moisture content after drying is 3.65%; The dry balls were roasted at 870°C for 30 minutes, and the roasted clinker was crushed until the particle size passed a 120-mesh sieve, accounting for 82.02%. The liquid-solid rati...
Embodiment 2
[0045]Take 1kg of sodiumized roasting water leaching vanadium tailings, the vanadium content is 0.88%, and the vanadium-titanium magnetite particle size is 82.30% 0.4kg through a 120 mesh sieve, and the two are evenly mixed and dried until the moisture content is 4.93%. Mixture 1 is obtained; mixture 1 and sodium carbonate are mixed according to the mass ratio of sodium and vanadium elements of 0.8 to obtain mixture 2; the bonding solution is carried out according to the mass ratio of sodium hydroxide, humic acid and water of 0.1:1.0:11.0 According to the preparation of wet pellets with a water content of 15-20%, the bonding solution is mixed with the mixture 2 and the wet pellets are pressed to control the particle size of the wet pellets to 10-20mm, and the moisture content after drying is 1.05%. Dry balls were roasted at 800°C for 60 minutes, and the calcined clinker was crushed to a particle size of 82.36% through a 120-mesh sieve. The liquid-solid ratio was controlled at (...
Embodiment 3
[0047] Take 1kg of sodiumized roasting water leaching vanadium tailings, the vanadium content is 1.02%, take the converter vanadium slag with a particle size of 120 mesh sieve and the proportion is 81.35% 0.3kg, mix the two evenly and dry until the water content is 3.13%, to obtain a mixed Material 1; Mixture 1 and sodium carbonate are mixed according to the mass ratio of sodium and vanadium elements of 1.2 to obtain Mixture 2; the bonding solution is prepared according to the mass ratio of sodium hydroxide, humic acid and water at 0.1:1.0:15.0 According to the water content of the wet pellets is 15-20%, the bonding solution is mixed with the mixture 2 and the wet pellets are pressed, the particle size of the wet pellets is controlled to be 10-20mm, and the moisture content after drying is 0.52%; the dry pellets after drying Roast at 850°C for 50 minutes, the calcined clinker is crushed until the particle size exceeds 120 mesh sieve, accounting for 81.06%, the liquid-solid rati...
PUM
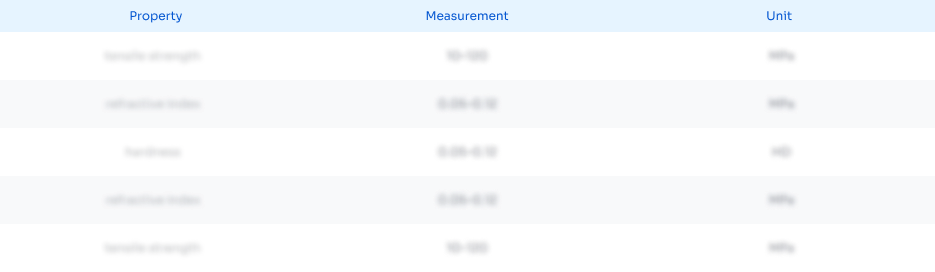
Abstract
Description
Claims
Application Information

- R&D
- Intellectual Property
- Life Sciences
- Materials
- Tech Scout
- Unparalleled Data Quality
- Higher Quality Content
- 60% Fewer Hallucinations
Browse by: Latest US Patents, China's latest patents, Technical Efficacy Thesaurus, Application Domain, Technology Topic, Popular Technical Reports.
© 2025 PatSnap. All rights reserved.Legal|Privacy policy|Modern Slavery Act Transparency Statement|Sitemap|About US| Contact US: help@patsnap.com