Continuous casting machine pouring device and pouring method
A pouring method and continuous casting machine technology, applied in the field of metallurgy, can solve the problems of short ladle molten steel pouring time, lower liquid level, adverse effects of molten steel purity, etc., achieve fully uniform molten steel temperature, and eliminate the effect of molten steel connection time difference
- Summary
- Abstract
- Description
- Claims
- Application Information
AI Technical Summary
Problems solved by technology
Method used
Image
Examples
Embodiment Construction
[0030] Embodiments of the pouring device and pouring method of the continuous casting machine according to the present invention will be described below with reference to the accompanying drawings. Those skilled in the art would recognize that the described embodiments can be modified in various ways or combinations thereof without departing from the spirit and scope of the invention. Accordingly, the drawings and description are illustrative in nature and not intended to limit the scope of the claims. Also, in this specification, the drawings are not drawn to scale, and like reference numerals denote like parts.
[0031] The pouring device of the continuous casting machine in this embodiment includes a double ladle turret, a tundish 5 , a crystallizer 9 , a slab support system 10 , a cooling system 11 , and a casting system 12 . Wherein, the double-ladle turret includes two single-arm turrets 4 arranged side by side, and any one-arm turret 4 can rotate around the slewing sup...
PUM
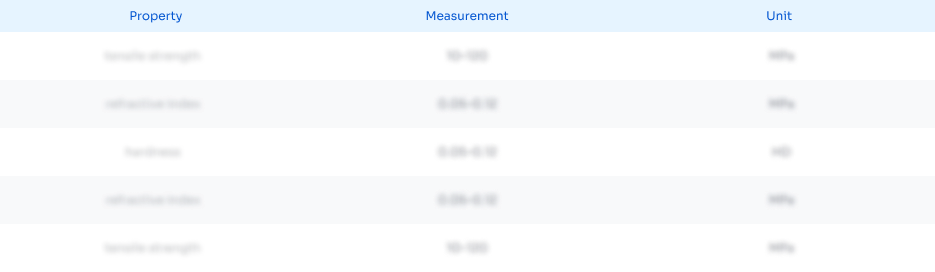
Abstract
Description
Claims
Application Information

- Generate Ideas
- Intellectual Property
- Life Sciences
- Materials
- Tech Scout
- Unparalleled Data Quality
- Higher Quality Content
- 60% Fewer Hallucinations
Browse by: Latest US Patents, China's latest patents, Technical Efficacy Thesaurus, Application Domain, Technology Topic, Popular Technical Reports.
© 2025 PatSnap. All rights reserved.Legal|Privacy policy|Modern Slavery Act Transparency Statement|Sitemap|About US| Contact US: help@patsnap.com