Digital measurement system and method for airplane structure deformation measurement and damage grading
A technology of aircraft structure and measurement method, applied in measurement devices, instruments, and optical devices, etc., can solve problems such as affecting the airworthiness of aircraft, reducing safety standards, and inability to draw qualitative conclusions, so as to maintain continuous airworthiness and safety. Pneumatic performance, avoiding human error, high degree of automation
- Summary
- Abstract
- Description
- Claims
- Application Information
AI Technical Summary
Problems solved by technology
Method used
Image
Examples
Embodiment 1
[0054] like figure 1 shown is a schematic diagram of the measurement system of the present invention when measuring aircraft components, a digital measurement system for aircraft structure deformation measurement and damage classification described in this embodiment, including a data acquisition and processing system 7, and a data acquisition and processing system 7. The laser tracker 6 and the lidar 3 are connected by communication.
[0055] There are multiple laser trackers 6 and laser radars 3 , all of which are connected to the data acquisition and processing system 7 in communication.
[0056] The digital measurement system also includes a flexible tool 5, such as image 3 As shown, the structure of the flexible tooling includes a support unit 10 and a positioning support body 11, wherein the height of the support unit 10 is adjustable for supporting and fixing the positioning support body 11; the positioning support body 11 is used for installing different bracket join...
Embodiment 2
[0058] like figure 2 As shown, it is a data processing flow chart of the digital measurement method for aircraft structure deformation measurement and damage classification according to the present invention, which specifically includes the following implementation steps:
[0059] (1) Arrange the flexible tooling 5 to support the fuselage structure; remove the nose landing gear and its lower mounting seat; then, use the positioning support body 11 supporting the tooling 5 to fix the key points of the fuselage structure (in this example, on the bulkhead The hole position of the mounting seat 4 under the landing gear); then remove the lower skin 8 (so that the laser tracker and lidar can detect the internal structure).
[0060] (2) Preparation before measurement. Adjust the relative positions of the laser tracker 6, the laser radar 3 and the component to be measured according to the measurement requirements and the characteristic properties of the workpiece to be measured. St...
PUM
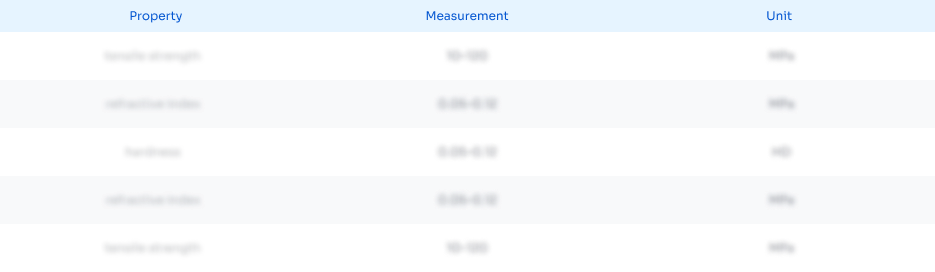
Abstract
Description
Claims
Application Information

- Generate Ideas
- Intellectual Property
- Life Sciences
- Materials
- Tech Scout
- Unparalleled Data Quality
- Higher Quality Content
- 60% Fewer Hallucinations
Browse by: Latest US Patents, China's latest patents, Technical Efficacy Thesaurus, Application Domain, Technology Topic, Popular Technical Reports.
© 2025 PatSnap. All rights reserved.Legal|Privacy policy|Modern Slavery Act Transparency Statement|Sitemap|About US| Contact US: help@patsnap.com