Forming Technology and Die of Axle Head of Hydraulic Bulging Drive Axle Housing
A technology of hydraulic bulging and forming process, which is used in forming tools, manufacturing tools, metal processing equipment and other directions to achieve the effect of saving forming costs
- Summary
- Abstract
- Description
- Claims
- Application Information
AI Technical Summary
Problems solved by technology
Method used
Image
Examples
Embodiment
[0039] figure 1 It is a schematic diagram and key dimensions of the hydraulic bulging drive axle housing of an electric vehicle: φ d0 =295mm,t 0 =10mm, φ d3 =125mm, φ d2 =115mm, φ d1 =88mm, t 1 =19mm and l 1 =668mm.
[0040] The invention provides a hydraulic bulging drive axle head forming process, that is, the preformed pipe fittings are obtained through the hydraulic bulging of the axle housing body (see figure 2 , l 2 ≥380mm) on the basis of shaft head forming, including three times of shaft end diameter reduction and four times of shaft end warm pushing, the specific process is as follows:
[0041] ① On the hydraulic machine, clamp the shaft tubes at both ends of the pipe for the first shaft end reduction, and the distance from the outer end surface of the clamping mold to the symmetrical centerline of the pipe is l j =580mm (see image 3 ), the outer diameter of the shaft end is reduced to φ after the diameter is reduced d2 =115mm, the distance between the in...
PUM
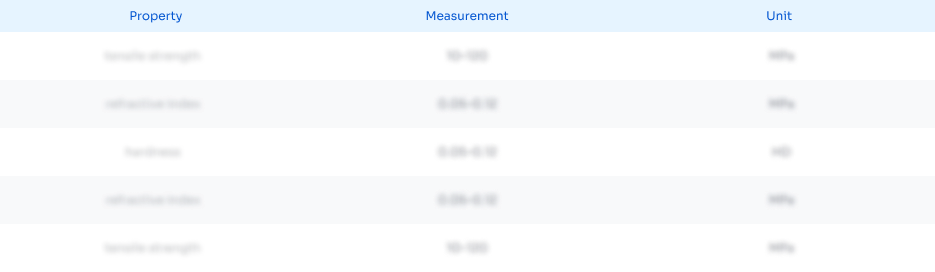
Abstract
Description
Claims
Application Information

- R&D
- Intellectual Property
- Life Sciences
- Materials
- Tech Scout
- Unparalleled Data Quality
- Higher Quality Content
- 60% Fewer Hallucinations
Browse by: Latest US Patents, China's latest patents, Technical Efficacy Thesaurus, Application Domain, Technology Topic, Popular Technical Reports.
© 2025 PatSnap. All rights reserved.Legal|Privacy policy|Modern Slavery Act Transparency Statement|Sitemap|About US| Contact US: help@patsnap.com