Proximity sensor inductance resolving method
A proximity sensor and inductance technology, applied in the field of proximity sensors, can solve problems such as poor low temperature indicators, difficult operation, and not suitable for mass production, so as to improve production efficiency and precision, avoid high and low temperature errors, and solve long-term measurement accuracy drift Effect
- Summary
- Abstract
- Description
- Claims
- Application Information
AI Technical Summary
Problems solved by technology
Method used
Image
Examples
Embodiment Construction
[0031] The method for calculating the inductance of the proximity sensor according to the present invention will be described in detail below with reference to the drawings and embodiments.
[0032] The method for solving the inductance of the proximity sensor in the present invention generates a digital waveform with adjustable amplitude and frequency through the excitation waveform module, and sends it to the proximity sensor after being driven by the coil excitation circuit; after the electrical feedback signal of the proximity sensor is detected and sampled, the The digital method is fed back to the calculation algorithm; the resistance and inductance parameters of the coil are directly separated by the calculation algorithm.
[0033] Such as figure 1 As shown, the main chip FPGA controls the DAC to generate a sine wave excitation signal through the SPI bus, and then excites the proximity sensor coil through the amplifier and current limiting. FPGA controls the conduction...
PUM
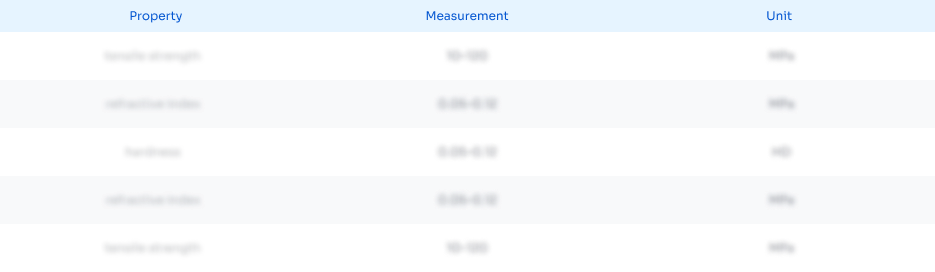
Abstract
Description
Claims
Application Information

- R&D Engineer
- R&D Manager
- IP Professional
- Industry Leading Data Capabilities
- Powerful AI technology
- Patent DNA Extraction
Browse by: Latest US Patents, China's latest patents, Technical Efficacy Thesaurus, Application Domain, Technology Topic, Popular Technical Reports.
© 2024 PatSnap. All rights reserved.Legal|Privacy policy|Modern Slavery Act Transparency Statement|Sitemap|About US| Contact US: help@patsnap.com