Digital image feeler vector coordinate transform calibration and error correction method and its device
A technology of coordinate transformation and error correction, which is applied in the field of vector coordinate transformation calibration and error correction of digital image probes and its devices, to meet the requirements of high-precision measurement, improve the accuracy of the entire field of view, and prevent measurement errors
- Summary
- Abstract
- Description
- Claims
- Application Information
AI Technical Summary
Problems solved by technology
Method used
Image
Examples
Embodiment Construction
[0038] The present invention will be described in further detail below in conjunction with the accompanying drawings.
[0039] see image 3 , the device of the present invention includes the X-axis guide rail and the precision grating 9, the Y-axis guide rail and the precision grating 8, the Z-axis guide rail and the precision grating 2, the Z-axis guide rail and the precision grating 2 driven by the motor perpendicular to each other along the X, Y, and Z directions. The grating 2 is sequentially installed with an area array CCD1, a continuous zoom optical lens 3 and a top ring light 4 from top to bottom. The entire axis, that is, the imaging optical axis, is perpendicular to the XOY plane, and a bottom is provided on the table formed by the X and Y axes Parallel contour light 6, glass bearing workbench 7 and calibration plate 5 of standard circle, said area array CCD1, optical lens 3, top ring light 4 and bottom parallel contour light 6 are coaxially installed.
[0040] The ...
PUM
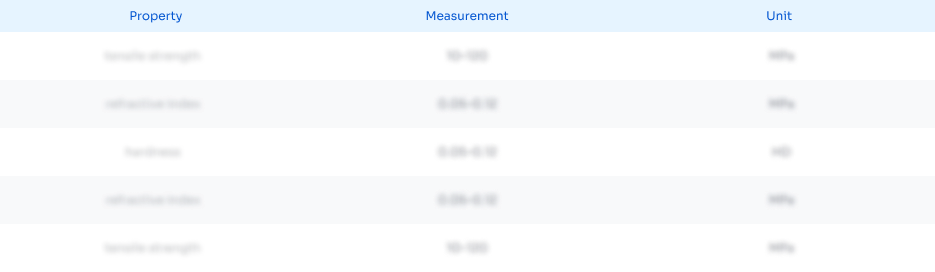
Abstract
Description
Claims
Application Information

- R&D Engineer
- R&D Manager
- IP Professional
- Industry Leading Data Capabilities
- Powerful AI technology
- Patent DNA Extraction
Browse by: Latest US Patents, China's latest patents, Technical Efficacy Thesaurus, Application Domain, Technology Topic, Popular Technical Reports.
© 2024 PatSnap. All rights reserved.Legal|Privacy policy|Modern Slavery Act Transparency Statement|Sitemap|About US| Contact US: help@patsnap.com