Cold heading forming process of automobile safety belt torsion shaft
A molding process and seat belt technology, applied in vehicle parts, railway car body parts, metal processing equipment, etc., can solve the problems of low material utilization rate, low productivity and high labor cost, improve material utilization rate and save processing costs. , The effect of improving machining accuracy and machining efficiency
- Summary
- Abstract
- Description
- Claims
- Application Information
AI Technical Summary
Problems solved by technology
Method used
Image
Examples
Embodiment 1
[0020] The cold heading forming process of the torsion shaft of the automobile safety belt described in this embodiment, such as figure 1 , figure 2 As shown, it includes the following steps:
[0021] a. cut material;
[0022] b. Preforming one end of the two end faces of the blank obtained in step a, and shaping the end face of the rod at the other end;
[0023] c. Upsetting the preformed end of the blank obtained in step b into a tooth blank;
[0024] d. Punching the tooth blank on the blank obtained in step c, so that the tooth is formed;
[0025] e. Upsetting the other end of the blank obtained in step d into a tooth blank with three haffle molds in the main mold;
[0026] f. The tooth blank obtained by upsetting the Huff die on the blank obtained in step e is punched to obtain a tooth shape.
[0027] In this embodiment, in order to realize the above-mentioned process, the above-mentioned process can be completed through five cold heading stations of a five-die...
PUM
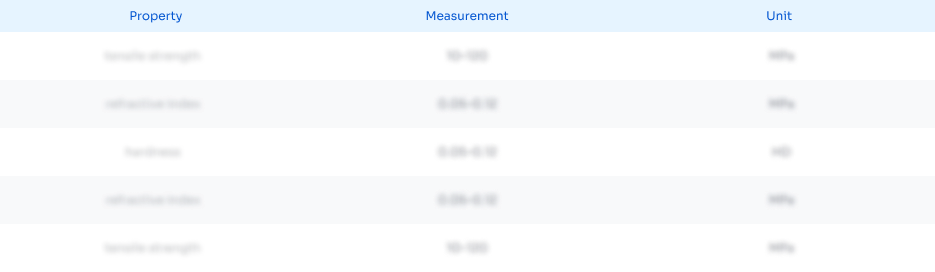
Abstract
Description
Claims
Application Information

- R&D Engineer
- R&D Manager
- IP Professional
- Industry Leading Data Capabilities
- Powerful AI technology
- Patent DNA Extraction
Browse by: Latest US Patents, China's latest patents, Technical Efficacy Thesaurus, Application Domain, Technology Topic, Popular Technical Reports.
© 2024 PatSnap. All rights reserved.Legal|Privacy policy|Modern Slavery Act Transparency Statement|Sitemap|About US| Contact US: help@patsnap.com