Preparing process of alloy steel forge piece
A preparation process and alloy steel technology, which is applied in the field of alloy steel casting, can solve the problems of energy consumption, resource consumption, cost consumption, etc., and achieve the effects of increasing strength, improving stress cracking resistance, and reducing energy consumption
- Summary
- Abstract
- Description
- Claims
- Application Information
AI Technical Summary
Problems solved by technology
Method used
Image
Examples
preparation example Construction
[0060] A preparation process of an alloy steel forging disclosed by the invention comprises the following process steps:
[0061] S1: cast steel ingot; the steel ingot contains the following components by weight percentage:
[0062] element C Si mn P S Cr Mo Ni Nb V Fe content(%) 0.30 0.2 0.6 0.001 0.001 0.75 0.35 1.45 0.01 0.02 96.618
[0063] S2: Transfer the cast steel ingot to an annealing furnace adjusted to 600°C at 600°C, and raise the temperature to 700°C for a uniform temperature.
[0064] S3: Forging, specifically including the following steps:
[0065] Step a: Transfer the steel ingot after step S2 into a forging heating furnace, and heat it to 1200°C;
[0066] Step b: remove the heated steel ingot from the forging furnace, and then carry out preliminary forging on the steel ingot with a small amount of deformation, and at the same time, use high-pressure water jetting to remove the scale on the surface of the steel in...
Embodiment 1
[0089] The difference between Embodiments 10-13 and Embodiment 1 is that each parameter setting during the forging process in step S3 is listed in the table below.
[0090]
[0091] The difference between Embodiments 14-17 and Embodiment 1 is that the parameter settings during the normalizing process in step S4 are listed in the table below.
[0092]
[0093] The difference between Examples 18-21 and Example 1 is that the parameter settings in the hydrogen expansion process in step S5 are listed in the following table.
[0094]
[0095]
[0096] The difference between Examples 22-25 and Example 1 is that the parameters set in the austenitizing process in step S6 are listed in the table below.
[0097]
[0098] The difference between Embodiments 26-25 and Embodiment 1 is that the parameter settings in the staged quenching and tempering process in step S7 are listed in the table below.
[0099]
PUM
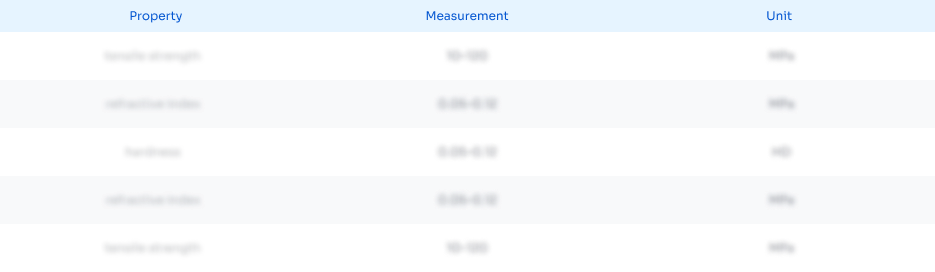
Abstract
Description
Claims
Application Information

- R&D
- Intellectual Property
- Life Sciences
- Materials
- Tech Scout
- Unparalleled Data Quality
- Higher Quality Content
- 60% Fewer Hallucinations
Browse by: Latest US Patents, China's latest patents, Technical Efficacy Thesaurus, Application Domain, Technology Topic, Popular Technical Reports.
© 2025 PatSnap. All rights reserved.Legal|Privacy policy|Modern Slavery Act Transparency Statement|Sitemap|About US| Contact US: help@patsnap.com