A kind of preparation technology of concrete prefabricated wallboard
A technology of prefabricated wallboard and preparation process, applied in the direction of manufacturing tools, walls, building components, etc., can solve the problems of prefabricated wallboard compressive strength reduction, prefabricated wallboard structure deformation, prefabricated wallboard cracks, etc., to prevent water evaporation Loss, improve the compressive strength, the effect of concrete uniformity
- Summary
- Abstract
- Description
- Claims
- Application Information
AI Technical Summary
Problems solved by technology
Method used
Image
Examples
Embodiment 1
[0044] A preparation process for concrete prefabricated wall panels, comprising the steps of:
[0045] S1: Mold preparation. refer to figure 1 , the mold includes side panels 1 , corner panels 2 and end panels 3 . The end plate 3 is placed horizontally on the ground, and the corner plate 2 and the side plate 1 are installed on the end plate 3 .
[0046] refer to figure 2 and image 3 , the shape of the side plate 1 is a cuboid, and the surface formed by the length and width is connected with the end plate 3 . A first bump 4 is integrally provided on one end surface of the side plate 1 defined by its height and width, and a groove 5 is formed on the other end surface along the length direction of the side plate 1 . The first protrusion 4 of the previous side panel 1 is plugged into the groove 5 of the rear side panel 1 . A waist-shaped hole 6 communicating with the groove 5 is provided on the outer wall of the groove 5 on the side plate 1 , and a threaded hole is provide...
Embodiment 2
[0068] The difference between embodiment 2 and embodiment 1 is that the raw materials of concrete include 210 parts of cement, 590 parts of coarse aggregate, 125 parts of fine aggregate, 365 parts of fly ash, 10 parts of calcium lignosulfonate, water 70 parts, 30 parts of fatty alcohol polyoxyethylene ether, 25 parts of acrylamide grafted copolymerized starch, and 3 parts of microsilica fume; the fly ash is Class I fly ash.
Embodiment 3
[0069] The difference between embodiment 3 and embodiment 1 is that the raw materials of concrete include 210 parts of cement, 590 parts of coarse aggregate, 125 parts of fine aggregate, 365 parts of fly ash, 10 parts of calcium lignosulfonate, water 70 parts, 30 parts of fatty alcohol polyoxyethylene ether, 25 parts of acrylamide grafted copolymerized starch, 21 parts of dipentaerythritol hexahydroxystearate, 3 parts of polycarboxylate superplasticizer and glyceryl stearate citrate 4 parts.
PUM
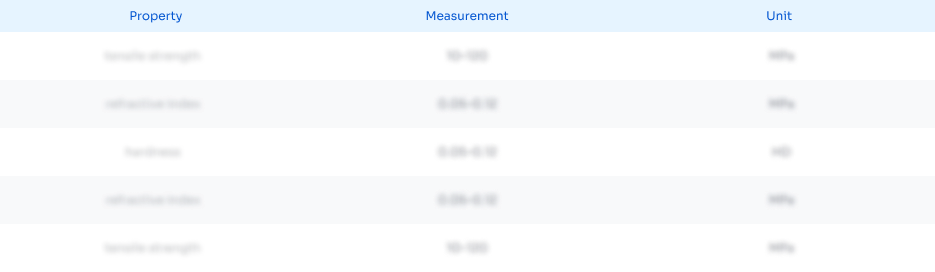
Abstract
Description
Claims
Application Information

- R&D
- Intellectual Property
- Life Sciences
- Materials
- Tech Scout
- Unparalleled Data Quality
- Higher Quality Content
- 60% Fewer Hallucinations
Browse by: Latest US Patents, China's latest patents, Technical Efficacy Thesaurus, Application Domain, Technology Topic, Popular Technical Reports.
© 2025 PatSnap. All rights reserved.Legal|Privacy policy|Modern Slavery Act Transparency Statement|Sitemap|About US| Contact US: help@patsnap.com