Method for removing hexavalent chromium in process of preparing cobalt nickel hydroxide from laterite-nickel ore
A technology of nickel cobalt hydroxide and laterite nickel ore, which is applied in the field of metallurgy and can solve problems such as unqualified products
- Summary
- Abstract
- Description
- Claims
- Application Information
AI Technical Summary
Problems solved by technology
Method used
Image
Examples
Embodiment 1
[0054] Taking a laterite nickel mine in Indonesia as the implementation object, the chromium content in the laterite nickel mine is 1.37%. The laterite nickel ore is made into a slurry with a concentration of 28wt%, and the first reducing agent is added to the laterite nickel ore slurry, specifically a composite agent with a ratio of sulfur to pyrite of 1:1, which is mixed with the total amount of the laterite nickel ore. The mass ratio of chromium is 1:1. Preheat to 200°C, then heat up, and carry out high-pressure acid leaching under the conditions of reaction temperature 250°C, acid ore ratio 200Kg / t, and reaction time 1h. After high-pressure leaching, the concentration of hexavalent chromium is less than 0.5mg / L. The leaching rates were 95.25% and 91.04%, respectively.
Embodiment 2
[0056] The difference from Example 1 is only that the chromium content in the laterite nickel ore is 2.14%, the first reducing agent is sulfur alone, the mass ratio of the first reducing agent to the total chromium in the laterite nickel ore is 1:3, and the content of Ni and Co The leaching rates are 95.81% and 91.45% respectively; the concentration of hexavalent chromium after high pressure leaching is less than 0.5mg / L.
Embodiment 3
[0058] The difference from Example 1 is only that the chromium content in the laterite nickel ore is 2.42%, the ratio of sulfur to pyrite is 4:1, the reaction temperature is 250°C, and the leaching rates of Ni and Co are 97.14% and 96.45% respectively; After high pressure leaching, the concentration of hexavalent chromium is <0.5mg / L.
PUM
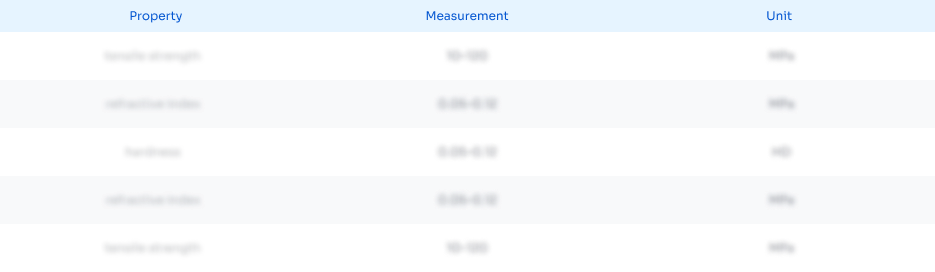
Abstract
Description
Claims
Application Information

- Generate Ideas
- Intellectual Property
- Life Sciences
- Materials
- Tech Scout
- Unparalleled Data Quality
- Higher Quality Content
- 60% Fewer Hallucinations
Browse by: Latest US Patents, China's latest patents, Technical Efficacy Thesaurus, Application Domain, Technology Topic, Popular Technical Reports.
© 2025 PatSnap. All rights reserved.Legal|Privacy policy|Modern Slavery Act Transparency Statement|Sitemap|About US| Contact US: help@patsnap.com