Inner heat insulation layer 3D printing system and method for solid rocket engine
A solid rocket and 3D printing technology, applied in 3D object support structures, household components, additive manufacturing, etc., to achieve high-precision manufacturing, relatively low price, and fast signal response
- Summary
- Abstract
- Description
- Claims
- Application Information
AI Technical Summary
Problems solved by technology
Method used
Image
Examples
Embodiment Construction
[0027] The present invention will be described in further detail below in conjunction with the accompanying drawings and specific embodiments.
[0028] Such as figure 1 and figure 2 As shown, a 3D printing system for the inner thermal insulation layer of a solid rocket motor includes a printing head, a photocuring device, a feeding device, a displacement amplification mechanism and a control system. Mechanismally, the control system is connected with the displacement amplification mechanism to control the movement of the displacement amplification mechanism. The print head includes a piezoelectric drive device, a striker, an air pressure control device, and a temperature control device. The feeding device includes an air compressor, Air pressure valve, storage tank. One or more print heads are used to form an array. The displacement amplification mechanism is a multi-degree-of-freedom mechanical arm. The light curing device is an ultraviolet light source.
[0029] A 3D p...
PUM
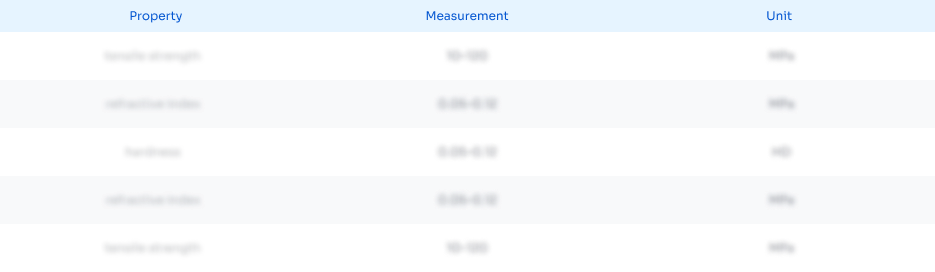
Abstract
Description
Claims
Application Information

- R&D
- Intellectual Property
- Life Sciences
- Materials
- Tech Scout
- Unparalleled Data Quality
- Higher Quality Content
- 60% Fewer Hallucinations
Browse by: Latest US Patents, China's latest patents, Technical Efficacy Thesaurus, Application Domain, Technology Topic, Popular Technical Reports.
© 2025 PatSnap. All rights reserved.Legal|Privacy policy|Modern Slavery Act Transparency Statement|Sitemap|About US| Contact US: help@patsnap.com