A Forging Process of E2 Vertical Roller
A technology of forging forming and process, which is applied in the field of forging forming process of E2 vertical roll, which can solve the problem that the quality of E2 vertical roll is difficult to meet the standard
- Summary
- Abstract
- Description
- Claims
- Application Information
AI Technical Summary
Problems solved by technology
Method used
Image
Examples
Embodiment 1
[0048] The E2 vertical roll is produced by the above process, and its specifications are: φ1360×720×2875mm. The specific forging process is as follows:
[0049] S11: Ingot heating, the heating temperature range is 1210-1230°C.
[0050] S12: out of the furnace, the whole ingot is upsetting H≤1200mm, and the FM method is drawn to 1200mm 2 , return to the furnace for homogenization, the homogenization temperature is 1220°C, and the time is 10h to obtain one upsetting and one drawing billet;
[0051] S12: out of the furnace, upsetting H≤1100mm, FM method drawing to 1400mm 2 , and then flatten the anvil and pull it to 1200mm 2 , return to the furnace for homogenization, the homogenization temperature is 1200 ° C, and the time is 2 to 4 h to obtain two upsetting and two drawing billets;
[0052] S13: out of the oven, upsetting H≤1100mm, FM method drawing to 1400mm 2 , and then flatten the anvil and pull it to 1200mm 2 , return to the furnace for homogenization, the homogenizatio...
PUM
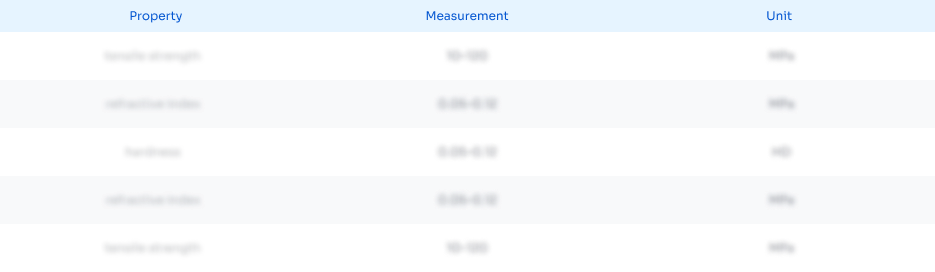
Abstract
Description
Claims
Application Information

- R&D
- Intellectual Property
- Life Sciences
- Materials
- Tech Scout
- Unparalleled Data Quality
- Higher Quality Content
- 60% Fewer Hallucinations
Browse by: Latest US Patents, China's latest patents, Technical Efficacy Thesaurus, Application Domain, Technology Topic, Popular Technical Reports.
© 2025 PatSnap. All rights reserved.Legal|Privacy policy|Modern Slavery Act Transparency Statement|Sitemap|About US| Contact US: help@patsnap.com