Smelting method for high-surface-quality IF steel
A smelting method and a high-surface technology, applied in the smelting field, can solve the problems of reduced life of the converter lining, insufficient heat source, increased risk of inclusions, etc.
- Summary
- Abstract
- Description
- Claims
- Application Information
AI Technical Summary
Problems solved by technology
Method used
Examples
Embodiment 1
[0057] Smelting steel type M3A35, after the molten iron is extracted from vanadium and desulfurized, the semi-steel is put into the steelmaking converter. Temperature: 655ppm, temperature 1656°C, no lime was added during the tapping process, and slag adjusting agent was not added to the small platform behind the furnace; the temperature of the LF furnace was 1622°C before heating, heated for 8 minutes, and 481kg of lime and 164kg of slag foaming agent were added during the heating process , No slagging agent was added at the departure station, the departure temperature was 1642°C; the RH treatment was 32 minutes and 56 seconds, the O activity after cyclic decarburization was 306.35ppm, 404kg of slagging agent was added before departure, the departure temperature was 1598°C, The Als content is 0.0353%, and the Als content of the finished molten steel is 0.038%.
[0058] Actual implementation results: 1. Add 645kg of slag to the ladle before the molten steel enters the RH proces...
Embodiment 2
[0060] Smelting steel type M3A30, after the molten iron is extracted from vanadium and desulfurized, the semi-steel enters the steelmaking converter. Temperature: 713ppm, temperature 1640°C, no lime was added during the tapping process, and slag adjusting agent was not added to the small platform behind the furnace; the temperature of the LF furnace was 1580°C before heating, heated for 17 minutes, and 650kg of lime and 116kg of slag foaming agent were added during the heating process , no slagging agent was added at the departure station, the departure temperature was 1645°C; the RH treatment was 28 minutes and 29 seconds, the O activity after cyclic decarburization was 312.18ppm, 600kg of slagging agent was added before departure, the departure temperature was 1583°C, The Als content is 0.036%, and the Als content of the finished molten steel is 0.037%.
[0061] Actual implementation effect: 1. Add 766kg of slag to the ladle before the molten steel enters the RH process, whi...
Embodiment 3
[0063]Smelting steel type M3A30, after the molten iron is extracted from vanadium and desulfurized, the semi-steel enters the steelmaking converter. Temperature: 575ppm, temperature 1657°C, no lime was added during the tapping process, and no slag adjusting agent was added to the small platform behind the furnace; the temperature of the LF furnace was 1647°C before heating, heated for 10 minutes, and 383kg of lime and 200kg of slag foaming agent were added during the heating process , No slagging agent was added at the departure station, the departure temperature was 1622°C; the RH treatment was 30 minutes and 14 seconds, the O activity after cyclic decarburization was 334.507ppm, 505kg of slagging agent was added before departure, the departure temperature was 1593°C, The Als content is 0.0314%, and the Als content of the finished molten steel is 0.031%.
[0064] Actual implementation results: 1. Add 645kg of slag to the ladle before the molten steel enters the RH process, wh...
PUM
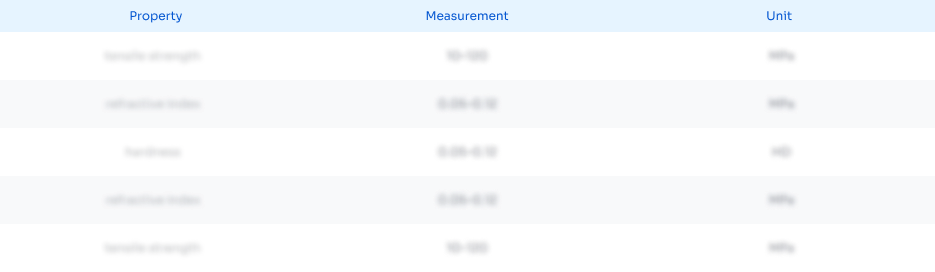
Abstract
Description
Claims
Application Information

- R&D Engineer
- R&D Manager
- IP Professional
- Industry Leading Data Capabilities
- Powerful AI technology
- Patent DNA Extraction
Browse by: Latest US Patents, China's latest patents, Technical Efficacy Thesaurus, Application Domain, Technology Topic, Popular Technical Reports.
© 2024 PatSnap. All rights reserved.Legal|Privacy policy|Modern Slavery Act Transparency Statement|Sitemap|About US| Contact US: help@patsnap.com