Preparation method of polyacetal resin
A technology of polyacetal resin and acetals, which is applied in the field of polyacetal resin and its preparation, can solve the problems of urgent development of inactivation process, reduction of mechanical properties of polyacetal resin, limitation of application scenarios, etc., to achieve effective splicing, The effect of simple inactivation process and simple process operation
- Summary
- Abstract
- Description
- Claims
- Application Information
AI Technical Summary
Problems solved by technology
Method used
Image
Examples
Embodiment 1
[0062] First, a certain amount of phosphotungstic acid is dissolved in methyl formate to obtain a solution with a concentration of 0.1wt%; paraformaldehyde, the methyl formate solution of phosphotungstic acid as a polymerization catalyst, and formaldehyde as a chain transfer agent Acetal and 1,3-dioxolane as a comonomer were supplied to the first continuous stirring and kneading type reactor (manufactured by List, Co-Rotating Processor (CRP) series: diameter 60mm , L / D (length-to-diameter ratio) = 18) continuous supply of the main feeding port, at 80 ° C continuous polymerization reaction. When the polymerization conversion rate is 60%, a mixed solution of pentaerythritol tetraglycidyl ether: 1,3-dioxolane = 1:1.5 is put into the feeding port at the rear of the reactor at 500g / h, and the mixture is added at 80 ℃ for further polymerization to obtain crude polyacetal powder.
[0063] Put the crude polyacetal powder and the deactivator sulfamethoxazole in a ratio of 100:1, that ...
Embodiment 2
[0069] The polyacetal resin is prepared by the method in Example 1, the difference is that when the polymerization conversion rate is 75%, it is pentaerythritol tetraglycidyl ether: 1 , 3-dioxolane=1:4 mixture; the temperature of the first continuous stirring and kneading reactor was changed from 80°C to 85°C; the temperature of the second continuous stirring and kneading reactor was changed from 100°C to 120°C , the rotation speed was changed from 30rpm to 50rpm, and the residence time was changed from 3min to 5min; the deactivator was replaced by 5-phenyl-1,3,4-oxadiazole-2-thiol from sulfamethoxazole; the deactivator and The ratio of crude polyacetal powder changed from 1:100 to 1:500.
Embodiment 3
[0071] The polyacetal resin is prepared by the method in Example 1, the difference is that when the polymerization conversion rate is 70%, it is pentaerythritol tetraglycidyl ether: 1 , 3-dioxolane=1:0.25 mixture; the temperature of the first continuous stirring and kneading reactor was changed from 80°C to 90°C; the temperature of the second continuous stirring and kneading reactor was changed from 100°C to 130°C , the rotation speed was changed from 30rpm to 60rpm, the residence time was changed from 3min to 8min; the ratio of deactivator to crude polyacetal powder was changed from 1:100 to 1:1000. The vacuum degree of each vacuum zone was replaced by 5 mbar to 10 mbar.
PUM
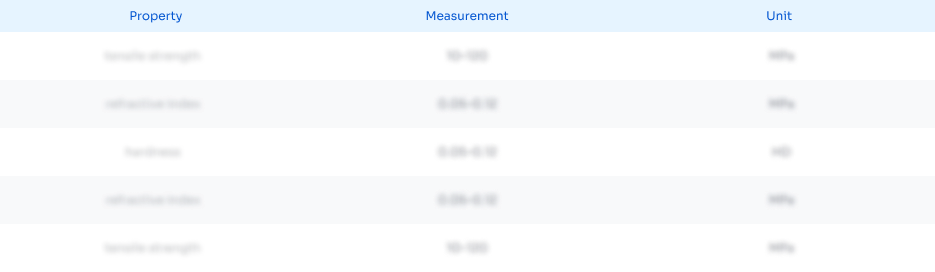
Abstract
Description
Claims
Application Information

- R&D
- Intellectual Property
- Life Sciences
- Materials
- Tech Scout
- Unparalleled Data Quality
- Higher Quality Content
- 60% Fewer Hallucinations
Browse by: Latest US Patents, China's latest patents, Technical Efficacy Thesaurus, Application Domain, Technology Topic, Popular Technical Reports.
© 2025 PatSnap. All rights reserved.Legal|Privacy policy|Modern Slavery Act Transparency Statement|Sitemap|About US| Contact US: help@patsnap.com