Aluminum alloy ingot and production technology thereof
An aluminum alloy ingot casting and production process technology, which is applied in the field of aluminum rod casting, can solve the problems of scrapping the head and tail of aluminum rods, coarse grain phenomenon, and increased production costs, so as to reduce the scrapping rate, increase the strength of grain refinement, and improve the production cost. The effect of grain size
- Summary
- Abstract
- Description
- Claims
- Application Information
AI Technical Summary
Problems solved by technology
Method used
Image
Examples
Embodiment Construction
[0048] The present invention will be further described below in conjunction with specific embodiments. It should be understood that the following examples are only used to illustrate the present invention but not to limit the scope of the present invention.
[0049] The production technology of aluminum alloy ingot of the present invention comprises the steps:
[0050] Step 1, raw material smelting:
[0051] Aluminum ingots and aluminum plate scraps are put into a melting furnace for melting. The aluminum plate scraps are preferably 6-series extruded aluminum plates. The mass ratio of aluminum ingots and aluminum plate scraps is A, and the raw material melting temperature is 680°C-730°C.
[0052] Step 2. Primary refining and slag removal in the upper furnace:
[0053] Control the melting temperature at 720°C-740°C. After reaching the specified temperature, use conventional refining agent + argon for refining. The amount of refining agent used is 0.6-1.0kg / ton of molten alumi...
PUM
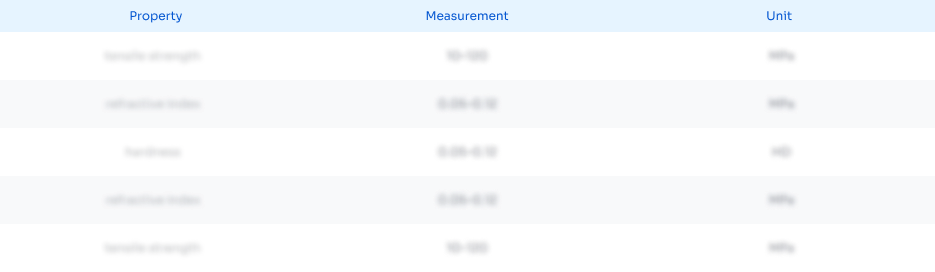
Abstract
Description
Claims
Application Information

- Generate Ideas
- Intellectual Property
- Life Sciences
- Materials
- Tech Scout
- Unparalleled Data Quality
- Higher Quality Content
- 60% Fewer Hallucinations
Browse by: Latest US Patents, China's latest patents, Technical Efficacy Thesaurus, Application Domain, Technology Topic, Popular Technical Reports.
© 2025 PatSnap. All rights reserved.Legal|Privacy policy|Modern Slavery Act Transparency Statement|Sitemap|About US| Contact US: help@patsnap.com