Glass optical fiber surface treating agent, alkali-resistant glass optical fiber and light-transmitting concrete prefabricated part
A surface treatment agent and light-transmitting concrete technology, which is applied in the field of glass optical fiber surface treatment agent, alkali-resistant glass optical fiber and light-transmitting concrete prefabricated parts, can solve the problems of reduced concrete strength, poor light transmission, and poor light guide. To achieve the effect of preventing corrosion, improving polarity and good compatibility
- Summary
- Abstract
- Description
- Claims
- Application Information
AI Technical Summary
Problems solved by technology
Method used
Image
Examples
Embodiment 1
[0037] The preparation method of alkali-resistant glass optical fiber in the present embodiment is:
[0038] (1) Hydrochloric acid and citric acid with a concentration of 0.08g / L are configured into an acid solution according to a weight ratio of 10:6, and the glass optical fiber is immersed in the acid solution for 20 minutes to complete the acidification treatment;
[0039] (2) According to parts by weight, prepare 100 parts of ethylene vinyl acetate copolymer emulsions, 8 parts of silane coupling agent KH550, 5 parts of film formers, 5 parts of sodium dodecylbenzenesulfonate, 5 parts of emulsified paraffin and 180 parts 2 parts deionized water, mixed and configured as a surface treatment agent, wherein the film-forming agent is a mixture of acrylic resin polyurethane copolymer resin and polyvinyl alcohol with a weight ratio of 10:2, and the surface treatment agent is sprayed on the glass during the preparation of the glass optical fiber. The surface of the optical fiber is ...
Embodiment 2
[0041] The preparation method of alkali glass optical fiber in the present embodiment is:
[0042] (1) Hydrochloric acid and citric acid with a concentration of 0.05g / L are configured into an acid solution according to a weight ratio of 10:5, and the glass optical fiber is immersed in the acid solution for 30 minutes to complete the acidification treatment;
[0043] (2) According to parts by weight, prepare 100 parts of ethylene vinyl acetate copolymer emulsions, 5 parts of silane coupling agent KH560, 6 parts of film formers, 5 parts of sodium dodecylbenzenesulfonate, 4 parts of emulsified paraffin and 150 parts 2 parts deionized water, mixed and configured as a surface treatment agent, wherein the film-forming agent is a mixture of acrylic resin polyurethane copolymer resin and polyvinyl alcohol with a weight ratio of 10:3, and the surface treatment agent is sprayed on the glass during the preparation of the glass optical fiber. The surface of the optical fiber is then heate...
Embodiment 3
[0045] The preparation method of alkali glass optical fiber in the present embodiment is:
[0046] (1) Hydrochloric acid and citric acid with a concentration of 0.1g / L are configured into an acid solution according to a weight ratio of 10:8, and the glass optical fiber is immersed in the acid solution for 10 minutes to complete the acidification treatment;
[0047] (2) According to parts by weight, prepare 100 parts of ethylene vinyl acetate copolymer emulsions, 9 parts of silane coupling agent KH570, 4 parts of film formers, 4 parts of sodium dodecylbenzenesulfonate, 5 parts of emulsified paraffin and 200 parts 2 parts deionized water, mixed and configured as a surface treatment agent, wherein the film-forming agent is a mixture of acrylic resin polyurethane copolymer resin and polyvinyl alcohol in a weight ratio of 10:1, and the surface treatment agent is sprayed on the glass during the preparation of the glass optical fiber. The surface of the optical fiber is then heated a...
PUM
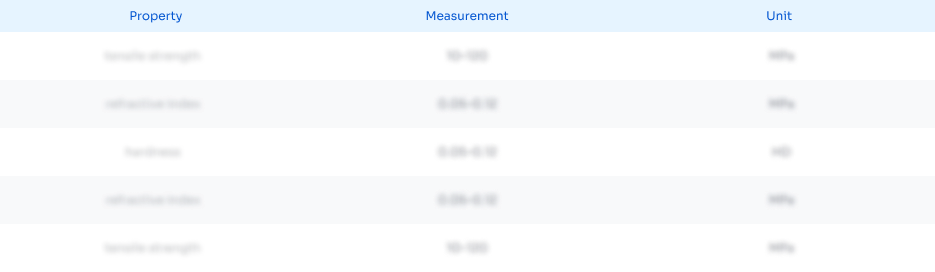
Abstract
Description
Claims
Application Information

- Generate Ideas
- Intellectual Property
- Life Sciences
- Materials
- Tech Scout
- Unparalleled Data Quality
- Higher Quality Content
- 60% Fewer Hallucinations
Browse by: Latest US Patents, China's latest patents, Technical Efficacy Thesaurus, Application Domain, Technology Topic, Popular Technical Reports.
© 2025 PatSnap. All rights reserved.Legal|Privacy policy|Modern Slavery Act Transparency Statement|Sitemap|About US| Contact US: help@patsnap.com