Wear-resistant pump body and manufacturing method thereof
A wear-resistant pump and wear-resistant layer technology, which is applied in the manufacture of tools, pumps, pump components, etc., can solve the problems of difficult lining forming, large kiln space, and high manufacturing cost, and achieve less assembly work and reduced overall length , the effect of good wear resistance
- Summary
- Abstract
- Description
- Claims
- Application Information
AI Technical Summary
Problems solved by technology
Method used
Image
Examples
Embodiment 1
[0061] like figure 1 , 2 , 3, Embodiment 1 of the present invention is a wear-resistant pump body of a medium-sized pump. The wear-resistant pump body includes a metal shell and a ceramic lining, wherein the metal shell includes a front shell 001 and a rear shell 005, and the water inlet 008 is arranged at On the front shell 001, the front shell 001 and the rear shell 005 are buckled on a plane A-A passing through the water outlet and connected together by bolts 009. The ceramic lining includes 12 pieces of different shapes arranged on the axial side of the wear-resistant pump body, sequentially The combined curved plate 003 also includes a fan-shaped front annular plate 0041 arranged on the side of the feed port of the wear-resistant pump body and a rear annular plate 0042 arranged on the other side. The front annular plate and the rear annular plate are respectively made of 6 fan-shaped boards are put together; such as image 3 Shown is a schematic diagram of the rear rin...
Embodiment 2
[0063] like Figure 4 As shown, Embodiment 2 of the present invention is a three-dimensional view after the curved panels of a large wear-resistant pump body are assembled, including 40 curved panels 003 of silicon nitride and silicon carbide, and the working surface area of a single curved panel is 0.1- 0.15 square meters, the axial projection angle of a single curved panel is 15°-20°, and the inner contour of all the curved panels 003 is two circles.
Embodiment 3
[0065] Embodiment 3 of the present invention is a medium-sized wear-resistant pump body, Figure 5 Shown is one of the curved panels 003, a plane 0032 coincident with the A-A plane is provided on the curved panel 003, and a protruding lip 0031 extending outward along the A-A plane is also provided to enhance the wear resistance of the place. The area of the curved panel is 0.13m 2 , the axial projection angle α is 62°.
PUM
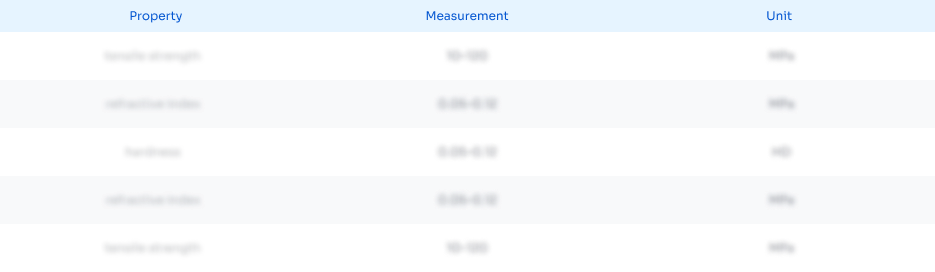
Abstract
Description
Claims
Application Information

- R&D
- Intellectual Property
- Life Sciences
- Materials
- Tech Scout
- Unparalleled Data Quality
- Higher Quality Content
- 60% Fewer Hallucinations
Browse by: Latest US Patents, China's latest patents, Technical Efficacy Thesaurus, Application Domain, Technology Topic, Popular Technical Reports.
© 2025 PatSnap. All rights reserved.Legal|Privacy policy|Modern Slavery Act Transparency Statement|Sitemap|About US| Contact US: help@patsnap.com