Method for efficiently utilizing complex molybdenum ore with wastewater self-circulation
A self-circulation, molybdenum ore technology, applied in the direction of improving process efficiency, can solve the problems of difficult economical and efficient disposal, large amount of waste water, etc.
- Summary
- Abstract
- Description
- Claims
- Application Information
AI Technical Summary
Problems solved by technology
Method used
Image
Examples
Embodiment 1
[0027] According to the ratio of liquid to solid 3:1.5:1, add dense supernatant: raffinate purification liquid: complex molybdenum ore, wet grind 50kg complex molybdenum ore to particle size -0.074mm>90%, thicken to underflow pulp concentration 30%, thick The supernatant returns to the grinding; dense underflow: the liquid after deamination is pulped at a ratio of 10:1, and then sent to oxygen pressure leaching, according to the H in the solution 2 SO 4 50g / L mixed with concentrated H 2 SO 4 , the leaching temperature is 160°C, the oxidizing agent is O 2 , the leaching process O 2 Partial pressure 0.3MPa, leaching time 3h, molybdenum oxidation rate 99%, molybdenum leaching rate 95%. Molybdenum was extracted with N235 in the leaching solution; the organic matter in the raffinate was naturally clarified + air flotation + ultrasonic demulsification + activated carbon adsorption and other deep degreasing, and the organic matter was reduced to 5ppm, and then Ca(OH) 2 Neutrali...
Embodiment 2
[0029] According to the liquid-solid ratio of 3:2:1, add dense supernatant: raffinate purification liquid: complex molybdenum ore, wet grind 50kg complex molybdenum ore to particle size -0.074mm>90%, thicken to underflow pulp concentration of 35%, dense The supernatant returns to the grinding; thick underflow: the liquid after deamination is pulped at 8:1 and sent to oxygen pressure leaching, according to the H in the solution 2 SO 4 40g / L mixed with concentrated H 2 SO 4 , the leaching temperature is 160°C, the oxidizing agent is O 2 , the leaching process O 2 Partial pressure 0.3MPa, leaching time 3h, molybdenum oxidation rate 99%, molybdenum leaching rate 93%. Molybdenum was extracted with N235 in the leaching solution; the organic matter in the raffinate was naturally clarified + air flotation + ultrasonic demulsification + fiber adsorption + activated carbon adsorption and other deep degreasing, and the organic matter was reduced to 8ppm, and then Ca(OH) 2 Neutraliz...
Embodiment 3
[0031] According to the liquid-solid ratio of 3:1:1, add dense supernatant: raffinate purification liquid: complex molybdenum ore, wet grind 50kg complex molybdenum ore to particle size -0.074mm>90%, thicken to bottom flow pulp concentration of 45%, dense The supernatant returns to the grinding; dense underflow: the liquid after deamination is pulped at 6:1 and sent to oxygen pressure leaching, according to the H in the solution 2 SO 4 40g / L mixed with concentrated H 2 SO 4 , the leaching temperature is 150°C, the oxidizing agent is O 2 , the leaching process O 2 The partial pressure is 0.3MPa, the leaching time is 3.5h, the molybdenum oxidation rate is 96%, and the molybdenum leaching rate is 93%. The leaching solution uses N235 to extract molybdenum; the raffinate is degreased by active carbon adsorption and the organic matter is reduced to 8ppm, and then Ca(OH) 2 Neutralize to pH 8.5, filter and separate the purified solution and return to the ore grinding; load the o...
PUM
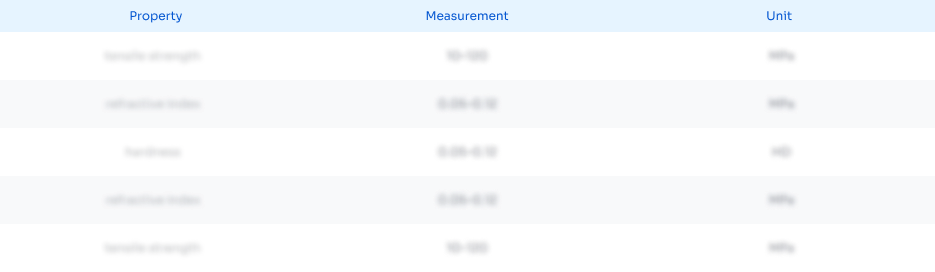
Abstract
Description
Claims
Application Information

- R&D Engineer
- R&D Manager
- IP Professional
- Industry Leading Data Capabilities
- Powerful AI technology
- Patent DNA Extraction
Browse by: Latest US Patents, China's latest patents, Technical Efficacy Thesaurus, Application Domain, Technology Topic, Popular Technical Reports.
© 2024 PatSnap. All rights reserved.Legal|Privacy policy|Modern Slavery Act Transparency Statement|Sitemap|About US| Contact US: help@patsnap.com