Automatic assembling and detection equipment for wire harness connector
A wire harness connector and automatic assembly technology, which is applied to the assembly/disassembly of contacts, continuity testing, metal processing equipment, etc., can solve the problems of low accuracy, easy fatigue, and high labor costs, and improve equipment production capacity. The effect of reducing manufacturing costs and labor costs
- Summary
- Abstract
- Description
- Claims
- Application Information
AI Technical Summary
Problems solved by technology
Method used
Image
Examples
Embodiment Construction
[0058] The present invention will be described in detail below with reference to the drawings and specific embodiments.
[0059] Reference Figure 2 to 4 As shown, the present invention provides an automatic assembly and testing equipment for a wire harness connector, including a mating assembly device 1, a tensile test device 2, a conduction test device 3, a linkage transfer manipulator 4, and a loading connector 82 The connector feeding device 5, the wire harness feeding device 6 for feeding the wire harness 81; the matching assembly device 1 is provided at one end of the wire harness feeding device 6, and is used to cooperate with the wire harness feeding device 6 to connect the wire harness 81 The terminal is inserted into the connector 82 to complete the assembly; the tensile test device 2 is arranged between the cooperating assembly device 1 and the conduction test device 3, and the linkage transfer manipulator 4 is used to simultaneously transfer the finished product on the...
PUM
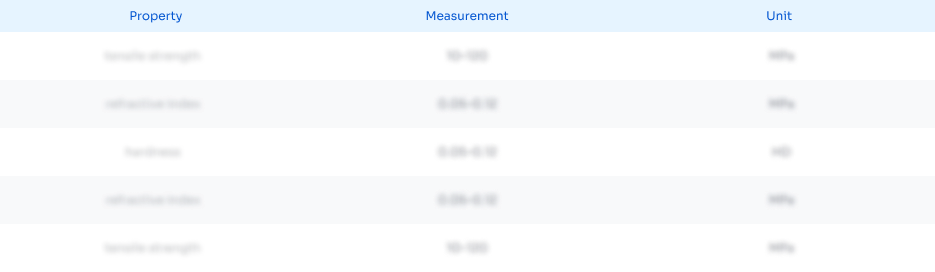
Abstract
Description
Claims
Application Information

- R&D Engineer
- R&D Manager
- IP Professional
- Industry Leading Data Capabilities
- Powerful AI technology
- Patent DNA Extraction
Browse by: Latest US Patents, China's latest patents, Technical Efficacy Thesaurus, Application Domain, Technology Topic, Popular Technical Reports.
© 2024 PatSnap. All rights reserved.Legal|Privacy policy|Modern Slavery Act Transparency Statement|Sitemap|About US| Contact US: help@patsnap.com