High-precision Collimator stepping motor control method capable of rapidly eliminating jitter
A technology of stepping motors and control methods, applied in the direction of motor generator control, control systems, electrical components, etc., can solve problems such as inability to achieve high-speed tracking focus, jitter, etc.
- Summary
- Abstract
- Description
- Claims
- Application Information
AI Technical Summary
Problems solved by technology
Method used
Image
Examples
Embodiment Construction
[0045] The present invention will be described in further detail below in conjunction with the embodiments.
[0046] This embodiment proposes a high-precision Collimator stepper motor control method with fast anti-shake, including the following steps:
[0047] S10: The CPU receives and analyzes the motion instructions sent by the upper computer, and obtains initial parameters, including the acceleration coefficient k a , target acceleration a m , target speed v m , startup speed v s , stop speed v e , start acceleration a s and stop acceleration a e , after the above parameters are determined, a unique S-shaped curve can be determined, and the starting speed of the stepper motor v s , stop speed v e , start acceleration a s and stop acceleration a e All are 0, so it is not necessary to calculate during control;
[0048] S20: Divide the displacement of the stepping motor into seven stages: acceleration section a, uniform acceleration section b, deceleration and accele...
PUM
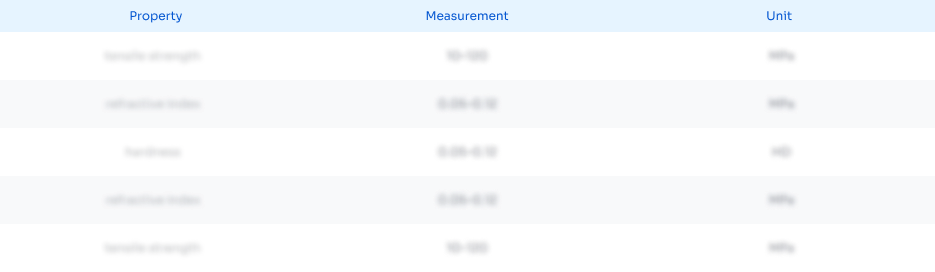
Abstract
Description
Claims
Application Information

- R&D
- Intellectual Property
- Life Sciences
- Materials
- Tech Scout
- Unparalleled Data Quality
- Higher Quality Content
- 60% Fewer Hallucinations
Browse by: Latest US Patents, China's latest patents, Technical Efficacy Thesaurus, Application Domain, Technology Topic, Popular Technical Reports.
© 2025 PatSnap. All rights reserved.Legal|Privacy policy|Modern Slavery Act Transparency Statement|Sitemap|About US| Contact US: help@patsnap.com