Silicon dioxide aerogel reinforced copper-based composite material and preparation method thereof
A technology of copper-based composite materials and silicon dioxide, applied in the field of particle-reinforced metal-based composite materials, metal materials and their preparation, to achieve the effects of improved mechanical properties, low cost, and excellent electrical and thermal conductivity
- Summary
- Abstract
- Description
- Claims
- Application Information
AI Technical Summary
Problems solved by technology
Method used
Image
Examples
Embodiment 1
[0036] Preparation of Cu-1wt.%SiO 2 Airgel composite material, its production process method is: (1) Cu-SiO 2 Preparation of airgel master alloy: batching-mixing-cold pressing; (2) preparation of composite materials: vacuum melting-casting.
[0037] The specific process is: according to Table 1 ingredient distribution. First, prepare Cu-10wt.%SiO 2 Airgel master alloy, mix electrolytic copper powder and silica airgel in a double-cone high-efficiency mixer for 12 hours, and then press the mixed powder under a hydraulic press with a pressure of 15MPa to form a block. Finally, T2 pure copper and Cu-10wt.% SiO prepared according to the target composition 2 The master alloy is placed in a vacuum medium frequency induction furnace and melted at 1200°C. After the pure copper is melted, the temperature is lowered to 1150°C before pouring. The properties of the prepared finished products are shown in Table 1.
Embodiment 2
[0039] Preparation of Cu-1.5wt.%SiO 2 Airgel composite material, its production process method is: (1) Cu-SiO 2 Preparation of airgel master alloy: batching-mixing-cold pressing; (2) preparation of composite materials: vacuum melting-casting.
[0040] The specific process is: according to Table 1 ingredient distribution. First, prepare Cu-10wt.%SiO 2 Airgel master alloy, mix electrolytic copper powder and silica airgel in a double-cone high-efficiency mixer for 12 hours, and then press the mixed powder under a hydraulic press with a pressure of 15MPa to form a block. Finally, T2 pure copper and Cu-10wt.% SiO prepared according to the target composition 2 The master alloy is placed in a vacuum medium frequency induction furnace and melted at 1250°C. After the pure copper is melted, the temperature is lowered to 1150°C before pouring. The properties of the prepared finished products are shown in Table 1.
Embodiment 3
[0042] Preparation of Cu-2wt.%SiO 2 Airgel composite material, its production process method is: (1) Cu-SiO 2Preparation of airgel master alloy: batching-mixing-cold pressing; (2) preparation of composite materials: vacuum melting-casting.
[0043] The specific process is: according to Table 1 ingredient distribution. First, prepare Cu-10wt.%SiO 2 Airgel master alloy, mix electrolytic copper powder and silica airgel in a double-cone high-efficiency mixer for 12 hours, and then press the mixed powder under a hydraulic press with a pressure of 15MPa to form a block. Finally, T2 pure copper and Cu-10wt.% SiO prepared according to the target composition 2 The master alloy is placed in a vacuum medium frequency induction furnace and melted at 1250°C. After the pure copper is melted, the temperature is lowered to 1150°C before pouring. The properties of the prepared finished products are shown in Table 1.
PUM
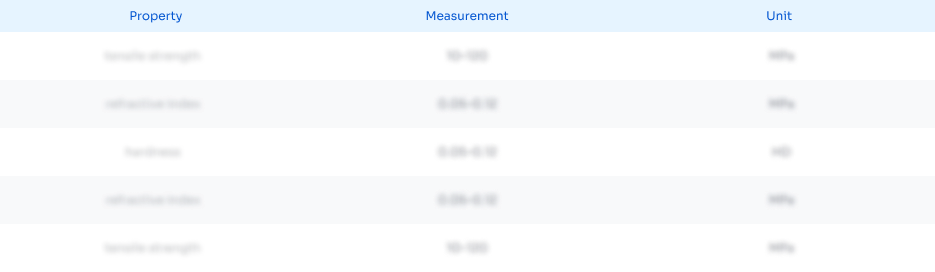
Abstract
Description
Claims
Application Information

- R&D Engineer
- R&D Manager
- IP Professional
- Industry Leading Data Capabilities
- Powerful AI technology
- Patent DNA Extraction
Browse by: Latest US Patents, China's latest patents, Technical Efficacy Thesaurus, Application Domain, Technology Topic, Popular Technical Reports.
© 2024 PatSnap. All rights reserved.Legal|Privacy policy|Modern Slavery Act Transparency Statement|Sitemap|About US| Contact US: help@patsnap.com