Zinc recovery method of blast furnace or shaft furnace and device adopted by zinc recovery method
A recovery device and recovery method technology, applied in the field of metallurgy, can solve the problems of solid waste pollution, waste of zinc resources, shortage of zinc resources, etc., and achieve the effects of less heat loss, reducing operating resistance, and solving the problem of direct production.
- Summary
- Abstract
- Description
- Claims
- Application Information
AI Technical Summary
Problems solved by technology
Method used
Image
Examples
Embodiment 1
[0041] A steel company, 30m 3 The blast furnace smelting furnace is used for the recovery and treatment of zinc-containing iron and steel dust. Due to the excessive zinc load, the furnace is often shut down for cleaning due to too much blast resistance. Each cleaning will remove several tons of zinc, and there are also solidified zinc in the gaps in the furnace wall. , Has a great influence on the life of the furnace body.
[0042] A method for recovering zinc from a blast furnace or a shaft furnace includes the following steps:
[0043] Step 1. Set up the annular flue:
[0044] During the overhaul of the blast furnace smelting furnace, according to the distribution area of zinc in the smelting furnace, 3 In the blast furnace at 750°C, there are 6 air outlets, and the flue gas ring flue 1 is set outside the blast furnace. The flue gas ring flue 1 is provided with 6 air holes of the same number and size as the blast furnace air holes. The air outlet of the blast furnace is connecte...
Embodiment 2
[0056] An iron and steel enterprise has an all-scrap steel-making shaft furnace. After the shaft furnace is equipped with a high-temperature gas producer, the gas temperature after the gas producer is higher than 1000℃, and the high-temperature gas returns to the shaft furnace to preheat the scrap, and the flue gas in the furnace is a reducing atmosphere , The scrap steel used in the shaft furnace is all crushed material, and the zinc content is relatively high. The steel-making shaft furnace can produce 90 tons of steel per hour. It is difficult to induce air during the operation. After the furnace is shut down, it is found that the charge is blocked due to zinc enrichment.
[0057] A method for recovering zinc from a shaft furnace includes the following steps:
[0058] Step 1. Set up the annular flue:
[0059] According to the distribution area of zinc in the shaft furnace smelting furnace, 8 air outlets are opened in the 720 ℃ area of the shaft furnace, and the flue gas ring f...
PUM
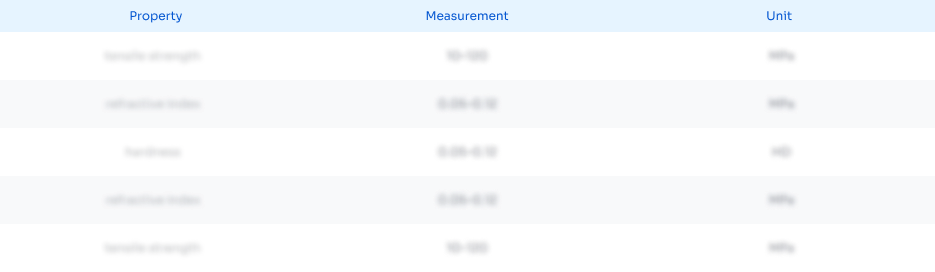
Abstract
Description
Claims
Application Information

- R&D Engineer
- R&D Manager
- IP Professional
- Industry Leading Data Capabilities
- Powerful AI technology
- Patent DNA Extraction
Browse by: Latest US Patents, China's latest patents, Technical Efficacy Thesaurus, Application Domain, Technology Topic, Popular Technical Reports.
© 2024 PatSnap. All rights reserved.Legal|Privacy policy|Modern Slavery Act Transparency Statement|Sitemap|About US| Contact US: help@patsnap.com