A weir type transition bag for thin strip continuous casting
A thin strip and continuous casting technology, which is applied in the field of iron and steel manufacturing, can solve the problems of small transition ladle capacity, uneven tapping temperature, cold steel blockage, etc., and achieve the goals of reducing slag inclusion defects, improving product quality, and increasing molten steel temperature Effect
- Summary
- Abstract
- Description
- Claims
- Application Information
AI Technical Summary
Problems solved by technology
Method used
Image
Examples
Embodiment Construction
[0028] In order to make the purpose, technical solutions and advantages of the embodiments of the present invention clearer, the technical solutions of the embodiments of the present invention will be clearly and completely described below. Apparently, the described embodiments are some, not all, embodiments of the present invention. Based on the described embodiments of the present invention, all other embodiments obtained by persons of ordinary skill in the art without creative efforts shall fall within the protection scope of the present invention.
[0029] Unless otherwise defined, the technical terms or scientific terms used in the present invention shall have the ordinary meanings understood by those having ordinary skill in the art to which the present invention belongs.
[0030] refer to figure 1 with figure 2 , which shows a weir-type transition bag for thin strip continuous casting according to an embodiment of the present invention.
[0031] Such as figure 1 ...
PUM
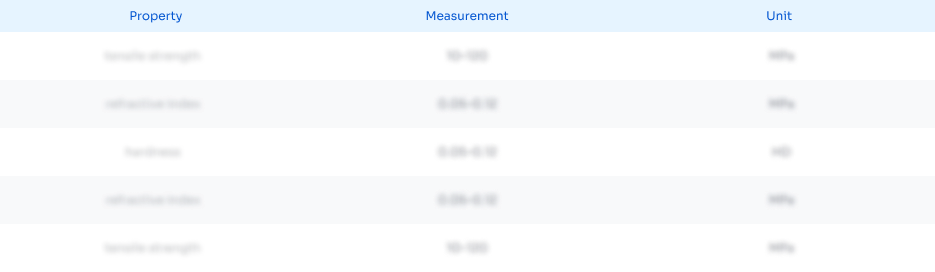
Abstract
Description
Claims
Application Information

- Generate Ideas
- Intellectual Property
- Life Sciences
- Materials
- Tech Scout
- Unparalleled Data Quality
- Higher Quality Content
- 60% Fewer Hallucinations
Browse by: Latest US Patents, China's latest patents, Technical Efficacy Thesaurus, Application Domain, Technology Topic, Popular Technical Reports.
© 2025 PatSnap. All rights reserved.Legal|Privacy policy|Modern Slavery Act Transparency Statement|Sitemap|About US| Contact US: help@patsnap.com