A special steel large bar rolling line and rolling method
A special steel and rolling line technology, which is applied in the field of special steel large bar rolling to achieve the effects of high-efficiency production, high production efficiency and production capacity, and improved production efficiency
- Summary
- Abstract
- Description
- Claims
- Application Information
AI Technical Summary
Problems solved by technology
Method used
Image
Examples
Embodiment Construction
[0028] The present invention is described in further detail below in conjunction with embodiment:
[0029] The present invention will be further described below, but the present invention is not limited in any way. Any transformation or replacement based on the teaching of the present invention belongs to the protection scope of the present invention.
[0030] The special steel bar rolling line of the present invention includes 1# pinch roll 1, rough rolling unit 2, hydraulic shear 3, head-off roller table 4, 2# pinch roll 5, middle finish rolling unit 6 and Double ruler cut 7.
[0031] Rough rolling unit 2, including 1#, 2#, 3#, 4#, 5#, 6# and 7# rolling mills which are alternately arranged vertically and horizontally (that is, 1# to 7# rolling mills are arranged in sequence along the bar rolling direction , 1# rolling mill is vertical rolling mill, 2# rolling mill is horizontal rolling mill, 3# rolling mill is vertical rolling mill, 4# rolling mill is horizontal rolling mil...
PUM
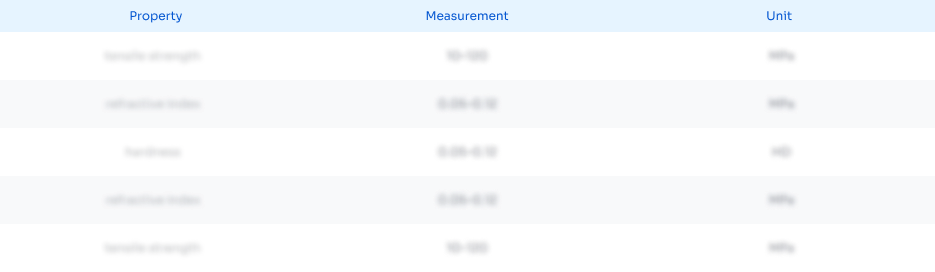
Abstract
Description
Claims
Application Information

- R&D Engineer
- R&D Manager
- IP Professional
- Industry Leading Data Capabilities
- Powerful AI technology
- Patent DNA Extraction
Browse by: Latest US Patents, China's latest patents, Technical Efficacy Thesaurus, Application Domain, Technology Topic, Popular Technical Reports.
© 2024 PatSnap. All rights reserved.Legal|Privacy policy|Modern Slavery Act Transparency Statement|Sitemap|About US| Contact US: help@patsnap.com