High-temperature-resistant self-lubricating wear-resistant composite material and preparation method thereof
A technology of composite materials and wear-resistant fillers, which is applied in the field of polymer wear-resistant materials, can solve problems such as adverse effects on the mechanical properties of composite materials, and achieve the effects of low wear, high mechanical properties, and excellent mechanical properties
- Summary
- Abstract
- Description
- Claims
- Application Information
AI Technical Summary
Problems solved by technology
Method used
Image
Examples
Embodiment 1
[0033] Stir 50kg of polyphenylene sulfide, 5kg of silicon carbide, 5kg of polytetrafluoroethylene, and 3kg of KH550 in a mixer, and add them into the main feeding hopper of twin-screw extrusion, and mix 30kg of PAN-based chopped carbon fibers and 10kg of pitch-based carbon fibers in the mixer. Stir evenly in the feeder and add to the side feeding hopper of the twin-screw extruder.
[0034] The above mixture was extruded and granulated in a twin-screw extruder with an aspect ratio of 65, and the temperature of each section was set at 280°C, 285°C, 285°C, 300°C, 300°C, 285°C, and 285°C. Rotational speed 150rpm / min.
Embodiment 2
[0036] Stir 80kg of polyetherimide, 5kg of boron nitride, 3kg of polytetrafluoroethylene, 2kg of graphite, and 1kg of KH550 in a mixer, add them to the main feeding hopper of twin-screw extrusion, and add 10kg of PAN-based chopped carbon fibers into the twin-screw In the side feed hopper of the screw extruder.
[0037] The above mixture was extruded and granulated in a twin-screw extruder with an aspect ratio of 65, and the temperature of each stage was set at 340°C, 355°C, 365°C, 370°C, 365°C, 365°C, and 365°C. Speed 110rpm / min.
Embodiment 3
[0039] Stir 55kg polyether ether ketone, 5kg silicon nitride, 5kg hollow glass microspheres, 15kg polytetrafluoroethylene, 5kg silicone oil, and 3kg KH560 in a mixer, add them to the main feeding hopper of twin-screw extrusion, and mix 10kg of PAN system Chopped carbon fibers, 5kg of pitch-based carbon fibers were stirred evenly in the mixer and added to the side feeding hopper of the twin-screw extruder.
[0040] The above mixture was extruded and granulated in a twin-screw extruder with an aspect ratio of 65, and the temperature of each stage was set at 360°C, 370°C, 380°C, 390°C, 385°C, 380°C, and 375°C. Rotational speed 150rpm / min.
PUM
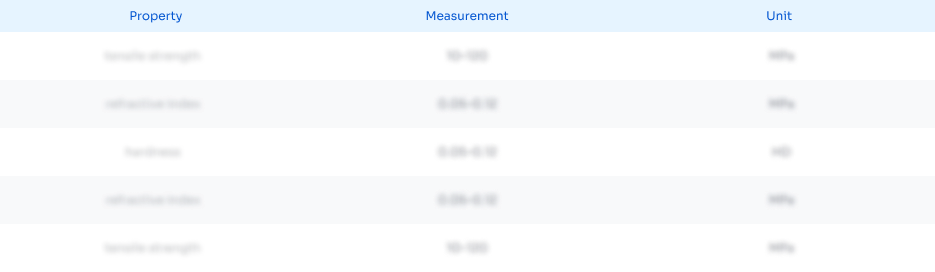
Abstract
Description
Claims
Application Information

- R&D Engineer
- R&D Manager
- IP Professional
- Industry Leading Data Capabilities
- Powerful AI technology
- Patent DNA Extraction
Browse by: Latest US Patents, China's latest patents, Technical Efficacy Thesaurus, Application Domain, Technology Topic, Popular Technical Reports.
© 2024 PatSnap. All rights reserved.Legal|Privacy policy|Modern Slavery Act Transparency Statement|Sitemap|About US| Contact US: help@patsnap.com