Process for horizontal coating of intrinsic silicon based on LPCVD technique
A process method, intrinsic silicon technology, applied in metal material coating process, gaseous chemical plating, sustainable manufacturing/processing, etc., can solve problems such as uneven coating, gas turbulence, increased burden, etc., and achieve grain size Uniformity, small disturbance, and the effect of reducing gas turbulence
- Summary
- Abstract
- Description
- Claims
- Application Information
AI Technical Summary
Problems solved by technology
Method used
Image
Examples
Embodiment 1
[0029] Step 1: Using as figure 2 In the way shown, the silicon wafers are loaded into the quartz boat by inserting the wafers horizontally, and the boat enters the quartz boat with the silicon wafers into the coated quartz tube at a set temperature of 500°C to keep the silicon wafers in a horizontal state. While entering the boat, 2000sccm-3000sccm of protective nitrogen gas is introduced.
[0030] Step 2: After the boat is in place, seal the furnace body, raise the temperature to 520°C, close the nitrogen inlet valve, and control the pressure in the furnace to a specific pressure of 500mtorr with a Roots pump. figure 1 It is the intrinsic silicon coating rate diagram at 520°C-620°C, and the corresponding temperature can be selected according to different rate requirements in this temperature range.
[0031] Step 3: Introduce silane into the air inlet of the furnace mouth and the furnace tail respectively, the silane flow rate is 100sccm-300sccm, and lasts for 5-10min. Among...
Embodiment 2
[0046] Step 1: Using as figure 2 In the way shown, the silicon wafers are loaded into the quartz boat by inserting the wafers horizontally, and the boat enters the quartz boat with the silicon wafers into the coated quartz tube at a set temperature of 500°C to keep the silicon wafers in a horizontal state. While entering the boat, 2000sccm-3000sccm of protective nitrogen gas is introduced.
[0047] Step 2: After the boat is in place, seal the furnace body, raise the temperature to 620°C, close the nitrogen inlet valve, and use a Roots pump to control the pressure in the furnace to a specific pressure of 450mtorr.
[0048] Step 3: Introduce silane into the air inlet of the furnace mouth and the furnace tail respectively, the silane flow rate is 100sccm-300sccm, and lasts for 5-10min. Among them, the furnace mouth is taken as Figure 4 The air intake is annular in the shown furnace mouth flange, and the annular air intake pipe 101 is bent into a semicircle and welded on the in...
Embodiment 3
[0055] Step 1: Using as figure 2 In the way shown, the silicon wafers are loaded into the quartz boat by inserting the wafers horizontally, and the boat enters the quartz boat with the silicon wafers into the coated quartz tube at a set temperature of 500°C to keep the silicon wafers in a horizontal state. While entering the boat, 2000sccm-3000sccm of protective nitrogen gas is introduced.
[0056] Step 2: After the boat is in place, seal the furnace body, raise the temperature to 580°C, close the nitrogen inlet valve, and at the same time, the Roots pump controls the pressure in the furnace to a specific pressure of 300mtorr.
[0057] Step 3: Introduce silane into the air inlet of the furnace mouth and the furnace tail respectively, the silane flow rate is 100sccm-300sccm, and lasts for 5-10min. Among them, the furnace mouth is taken as Figure 4 The air intake is annular in the shown furnace mouth flange, and the annular air intake pipe 101 is bent into a semicircle and we...
PUM
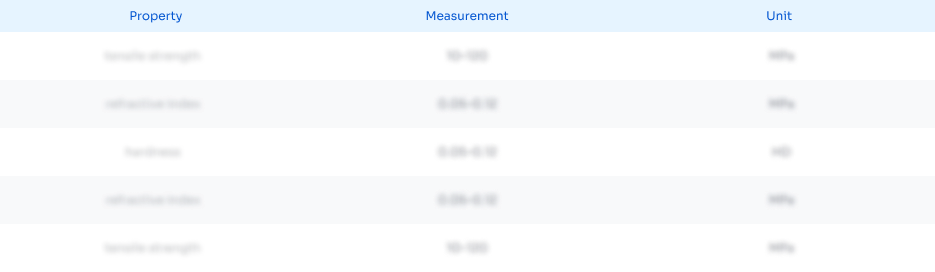
Abstract
Description
Claims
Application Information

- Generate Ideas
- Intellectual Property
- Life Sciences
- Materials
- Tech Scout
- Unparalleled Data Quality
- Higher Quality Content
- 60% Fewer Hallucinations
Browse by: Latest US Patents, China's latest patents, Technical Efficacy Thesaurus, Application Domain, Technology Topic, Popular Technical Reports.
© 2025 PatSnap. All rights reserved.Legal|Privacy policy|Modern Slavery Act Transparency Statement|Sitemap|About US| Contact US: help@patsnap.com