Automatic brazing equipment for copper pipes and joints and its control method
A copper tube and brazing technology, which is applied in the field of automatic brazing equipment for copper tubes and joints and its control, can solve the problems of unfavorable copper tube picking and placing, lower production efficiency, and no detection device, so as to improve the working environment of workers , save manpower and material resources, improve the effect of brazing quality
- Summary
- Abstract
- Description
- Claims
- Application Information
AI Technical Summary
Problems solved by technology
Method used
Image
Examples
Embodiment Construction
[0067] The present invention will be further described in detail below in conjunction with the accompanying drawings and specific embodiments.
[0068] Disclosed by the present invention is an automatic brazing equipment for copper pipes and joints, such as Figure 1 to Figure 20 Shown is a preferred embodiment of the brazing equipment of the present invention. The automatic brazing equipment includes a copper tube feeding mechanism 1, a copper tube feeding mechanism 2, a copper tube positioning mechanism 3, a joint feeding and fitting mechanism 4, a socket detection mechanism 5, a high frequency brazing machine 6, a blanking Mechanism 7, mobile platform mechanism 8 and control mechanism. The key and focus of the present invention are the copper pipe positioning mechanism 3, the joint feeding and fitting mechanism 4, and the socket detection mechanism 5. The other mechanisms are all auxiliary settings, or are designed to realize full automation, and are not required to be set...
PUM
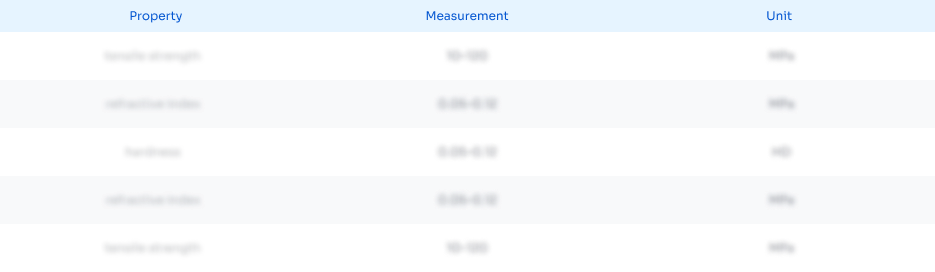
Abstract
Description
Claims
Application Information

- Generate Ideas
- Intellectual Property
- Life Sciences
- Materials
- Tech Scout
- Unparalleled Data Quality
- Higher Quality Content
- 60% Fewer Hallucinations
Browse by: Latest US Patents, China's latest patents, Technical Efficacy Thesaurus, Application Domain, Technology Topic, Popular Technical Reports.
© 2025 PatSnap. All rights reserved.Legal|Privacy policy|Modern Slavery Act Transparency Statement|Sitemap|About US| Contact US: help@patsnap.com