Fault diagnosis method for aero-engine control system sensor based on 3DCNN-JTFA
A technology for aero-engines and control systems, applied in general control systems, control/regulation systems, test/monitoring control systems, etc., and can solve problems such as data mismatches
- Summary
- Abstract
- Description
- Claims
- Application Information
AI Technical Summary
Problems solved by technology
Method used
Image
Examples
Embodiment Construction
[0070] Now in conjunction with embodiment, accompanying drawing, the present invention will be further described:
[0071] Embodiments of the present invention include the following steps:
[0072] Fault generator stage:
[0073] (1) The state variable model of the aeroengine is established by the component method, and the mathematical model of the aeroengine-sensor is established with the second-order inertial element as the mathematical model of the sensor;
[0074] The second order inertial elements are described as:
[0075]
[0076] Among them, ξ is the damping ratio of the sensor, w n is the natural frequency of the sensor, τ is the delay time;
[0077] The mathematical model of the aero-engine state variable is connected in series with the mathematical model of the sensor to form a mathematical model of the aero-engine control system;
[0078] (2) On the basis of the mathematical model of the aero-engine control system-sensor, through the analysis and simulation ...
PUM
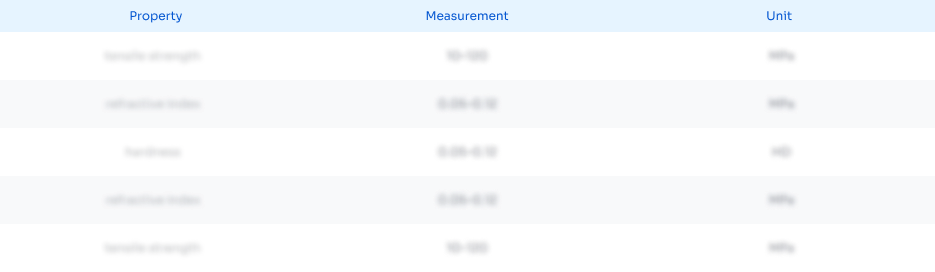
Abstract
Description
Claims
Application Information

- Generate Ideas
- Intellectual Property
- Life Sciences
- Materials
- Tech Scout
- Unparalleled Data Quality
- Higher Quality Content
- 60% Fewer Hallucinations
Browse by: Latest US Patents, China's latest patents, Technical Efficacy Thesaurus, Application Domain, Technology Topic, Popular Technical Reports.
© 2025 PatSnap. All rights reserved.Legal|Privacy policy|Modern Slavery Act Transparency Statement|Sitemap|About US| Contact US: help@patsnap.com