Method for selectively extracting valuable metals from waste lithium ion battery powder based on reduced sodium roasting phase conversion
A lithium-ion battery, sodium roasting technology, applied in the direction of battery recycling, process efficiency improvement, waste collector recycling, etc., can solve the problems of large consumption of reducing agent reagents, high production costs, many processes, etc., to reduce purification and removal The effect of low burden and low production cost
- Summary
- Abstract
- Description
- Claims
- Application Information
AI Technical Summary
Problems solved by technology
Method used
Image
Examples
Embodiment 1
[0024] Such as figure 1 As shown, this embodiment provides a method for selectively extracting valuable metals from spent lithium-ion battery powder based on the phase transformation of the reduced sodium roasted product, including the following steps:
[0025] (1) Using waste ternary battery powder as raw material, its main composition is: Li4.5wt%, Ni20.0wt%, Co7.6wt%, Mn11.7wt%, Cu0.09wt%, Fe0.03wt%, Al0.3wt% %, C28.5wt%. Mix waste ternary battery powder with sodium sulfate in molar ratio n Li :n Na2SO4 =1:1 mixing and ball milling for 1.5h to obtain the mixture.
[0026] (2) Put the mixture obtained in the step (1) in an electric furnace for reduction and sodium roasting at 750° C. for 1.5 hours to obtain calcined sand.
[0027] (3) The calcined sand obtained in step (2) is leached with pure water, and the liquid-solid ratio is 8:1, and reacted at 80° C. for 2 hours to obtain a lithium-containing leachate and conversion slag. The lithium-containing leachate can be used...
Embodiment 2
[0031] This embodiment provides a method for selectively extracting valuable metals from spent lithium-ion battery powder based on the phase transformation of reduced sodium-calcined products, including the following steps:
[0032] (1) Using waste ternary and lithium cobalt oxide mixed battery powder as raw material, control its main composition as Li6.57wt%, Ni5.93wt%, Co42.37wt%, Mn3.79wt%, Cu0.93wt%, Fe0.08wt% %, Al0.38wt%, C24.59wt%. Mix waste lithium battery powder with sodium sulfate in molar ratio n Li :n Na2SO4 =1:1.2 Mixing and ball milling for 1.5h to obtain a mixture.
[0033] (2) Put the mixture obtained in the step (1) in an electric furnace for reduction and sodium roasting at 700° C. for 3 hours to obtain calcined sand.
[0034] (3) The calcined sand obtained in step (2) is leached with pure water, and the liquid-solid ratio is 5:1, and reacted at 40° C. for 3 hours to obtain a lithium-containing leachate and conversion slag. The lithium-containing leachate ...
Embodiment 3
[0038] This embodiment provides a method for selectively extracting valuable metals from spent lithium-ion battery powder based on the phase transformation of reduced sodium-calcined products, including the following steps:
[0039] (1) Use waste ternary and lithium manganate mixed battery powder as raw material, control its main composition as Li6.25wt%, Ni5.23wt%, Co1.32wt%, Mn48.67wt%, Cu0.61wt%, Fe0.% , Al0.26wt%, C17.89wt%. Mix waste lithium battery powder with sodium sulfate in molar ratio n Li :n Na2SO4 = 1:1 mixing and ball milling for 2 hours to obtain a mixture.
[0040] (2) Put the mixture obtained in the step (1) in an electric furnace for reduction and sodium roasting at 700° C. for 4 hours to obtain calcined sand.
[0041](3) The calcined sand obtained in step (2) is leached with pure water, and the liquid-solid ratio is 6:1, and reacted at 80° C. for 3 hours to obtain lithium-containing leachate and conversion slag, which can be used to prepare lithium carbon...
PUM
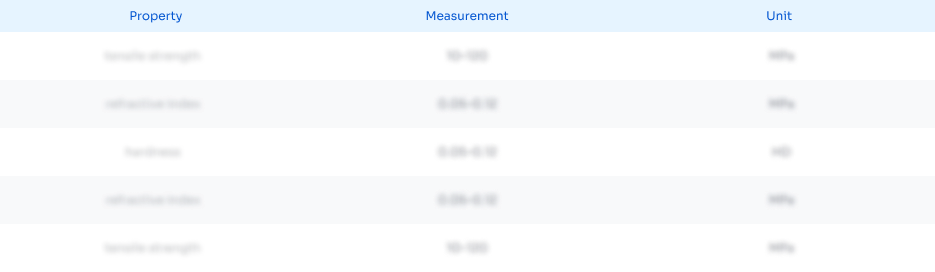
Abstract
Description
Claims
Application Information

- Generate Ideas
- Intellectual Property
- Life Sciences
- Materials
- Tech Scout
- Unparalleled Data Quality
- Higher Quality Content
- 60% Fewer Hallucinations
Browse by: Latest US Patents, China's latest patents, Technical Efficacy Thesaurus, Application Domain, Technology Topic, Popular Technical Reports.
© 2025 PatSnap. All rights reserved.Legal|Privacy policy|Modern Slavery Act Transparency Statement|Sitemap|About US| Contact US: help@patsnap.com