Self-learning model predictive control method for assembly of robot electronic components
A technology of model predictive control and electronic components, applied in the field of self-learning model predictive control, can solve the problems of small size and easy damage of electronic components, and achieve the effect of high precision and fast speed
- Summary
- Abstract
- Description
- Claims
- Application Information
AI Technical Summary
Problems solved by technology
Method used
Image
Examples
Embodiment Construction
[0024] The present invention will be further described below in conjunction with the accompanying drawings and specific embodiments.
[0025] like figure 1 As shown, the robotic electronic component assembly process includes the following steps:
[0026]Step 1. Construction of electronic component assembly feature knowledge base S01: Determine the specific weight, center of gravity, shape, density and other characteristics of electronic components, and then build an electronic component assembly feature knowledge base to determine the assembly characteristics in the robot assembly process. The size, direction and load change of angle and assembly force. The electronic components in this embodiment are RS-05K1002FT color ring resistors.
[0027] Step 2. Planning S02 of expected trajectory (position) of electronic component assembly: planning the expected trajectory (position) of electronic component assembly according to the sequence of electronic component assembly and the b...
PUM
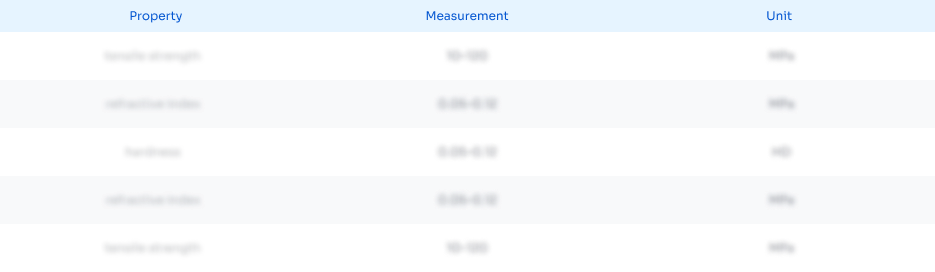
Abstract
Description
Claims
Application Information

- Generate Ideas
- Intellectual Property
- Life Sciences
- Materials
- Tech Scout
- Unparalleled Data Quality
- Higher Quality Content
- 60% Fewer Hallucinations
Browse by: Latest US Patents, China's latest patents, Technical Efficacy Thesaurus, Application Domain, Technology Topic, Popular Technical Reports.
© 2025 PatSnap. All rights reserved.Legal|Privacy policy|Modern Slavery Act Transparency Statement|Sitemap|About US| Contact US: help@patsnap.com