Alkaline flux-cored wire for pipeline girth welding and up-and-down feeding automatic welding
A technology of automatic welding and flux-cored wire, which is applied in the direction of welding medium, welding equipment, welding/cutting medium/material, etc., can solve the problems of low efficiency, achieve the effects of reducing defects, small transition particles, and strong arc force
- Summary
- Abstract
- Description
- Claims
- Application Information
AI Technical Summary
Problems solved by technology
Method used
Image
Examples
Embodiment Construction
[0028] The technical solutions of the present invention will be further described below in conjunction with specific examples, but the present invention is not limited to these examples.
[0029]A basic flux-cored wire used for pipeline ring welding and automatic welding from top to bottom. It is composed of a carbon steel sheath covering a flux-cored welding wire.
[0030] Table 1 Carbon steel skin component content
[0031] C Si mn Al 0.010-0.030 0.01-0.03 0.10-0.30 0.005~0.035 P S Fe 0.005-0.010 0.005-0.010 margin
[0032] The weight of the flux core accounts for 12.5% to 21.0% of the total weight of the welding wire. Table 2 shows the weight percentages of the flux core components in the examples except iron.
[0033] The specification of the welding wire of the present invention is 0.045-0.062 or 1.2mm-1.6mm.
[0034] The operability test uses the base metal X70 and X80 pipes, and the specifications and components are shown i...
PUM
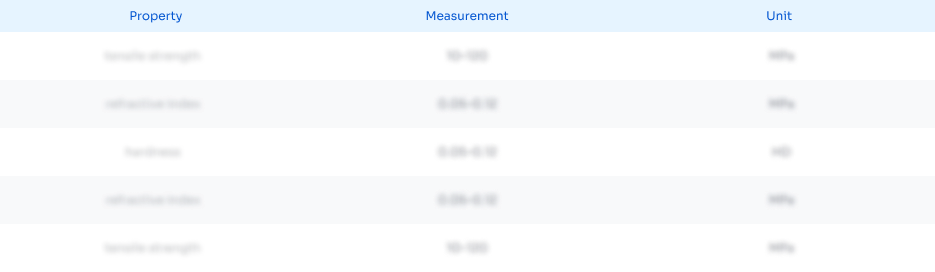
Abstract
Description
Claims
Application Information

- R&D
- Intellectual Property
- Life Sciences
- Materials
- Tech Scout
- Unparalleled Data Quality
- Higher Quality Content
- 60% Fewer Hallucinations
Browse by: Latest US Patents, China's latest patents, Technical Efficacy Thesaurus, Application Domain, Technology Topic, Popular Technical Reports.
© 2025 PatSnap. All rights reserved.Legal|Privacy policy|Modern Slavery Act Transparency Statement|Sitemap|About US| Contact US: help@patsnap.com