Position-based multi-hydraulic-cylinder coordination control method and device for stably outputting liquid
A coordinated control, multi-hydraulic cylinder technology, used in fluid pressure actuation devices, fluid pressure actuation system components, servo motors, etc., can solve the problems of output flow and pressure pulsation, and achieve small flow and pressure pulsation, reversing The effect of low time requirement and stable output
- Summary
- Abstract
- Description
- Claims
- Application Information
AI Technical Summary
Problems solved by technology
Method used
Image
Examples
Embodiment 1
[0028] Embodiment 1: The position-based multi-hydraulic cylinder coordinated control method for stable output of liquid is carried out as follows: before the n groups of hydraulic cylinders work, the strokes of the n groups of hydraulic cylinders are initialized, and the n groups of hydraulic cylinders are respectively in the At the starting point of the stroke, near the end point, (n-m+1) / (n-1) stroke, any group of hydraulic cylinders in the n groups of hydraulic cylinders is recorded as the m-th group of hydraulic cylinders, 1≤m≤n, m, n are natural numbers;
[0029] After the hydraulic cylinder strokes of each group of hydraulic cylinders are initialized, the hydraulic cylinders start to work, the mth group of hydraulic cylinders is in a stop waiting state (at the starting point of the stroke), and the other groups of hydraulic cylinders move normally. When the m+1th group of hydraulic cylinders is about to reach the stroke At the end point, the reversing valve controlling t...
Embodiment 2
[0030] Embodiment 2: As an optimization of the above embodiment, the position-based multi-hydraulic cylinder coordinated control method for the smooth output of liquid is carried out as follows: when n is three, before the three groups of hydraulic cylinders work, the first three groups The piston positions of the hydraulic cylinders are initialized. The initial states of the three groups of hydraulic cylinders are at the starting point, middle point, and end point of the stroke respectively. The piston of any one of the piston cylinders is at the end of the stroke, and the piston of any one of the piston cylinders in group III hydraulic cylinders 19 is at the midpoint of the stroke. Then, the three groups of hydraulic cylinders start to work.
[0031] Group II hydraulic cylinder 18 and Group III hydraulic cylinder 19 move normally, and the piston of any piston cylinder in Group I hydraulic cylinder 17 is in a stop waiting state (starting point of stroke). When the piston of t...
Embodiment 3
[0032] Embodiment 3: As an optimization of the above embodiment, the difference from Embodiment 2 is that the position-based multi-hydraulic cylinder coordinated control method for smooth output of liquid is carried out as follows: when n is four, at four Before the group of hydraulic cylinders work, the piston positions of the four groups of hydraulic cylinders are initialized first. The initial states of the four groups of hydraulic cylinders are at the starting point, end point, 2 / 3 stroke, and 1 / 3 stroke respectively, that is, group I The piston of any piston cylinder in the hydraulic cylinder 17 is at the starting point of the stroke, the piston of any piston cylinder in the group II hydraulic cylinder 18 is at the end of the stroke, and the piston of any piston cylinder in the group III hydraulic cylinder 19 is at the 2 / 3 stroke At the position, the piston of any one of the hydraulic cylinders in the IV group is at 1 / 3 of the stroke, and then the four groups of hydraulic ...
PUM
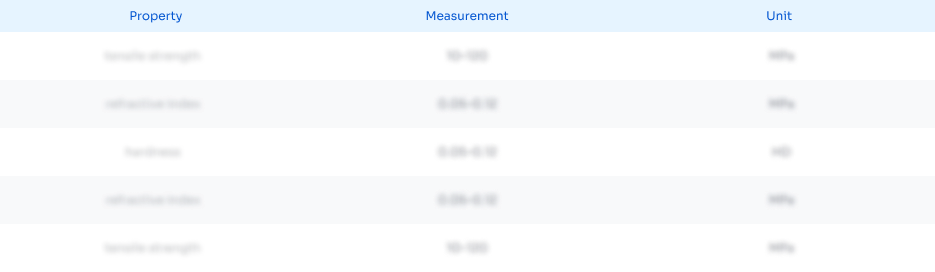
Abstract
Description
Claims
Application Information

- R&D
- Intellectual Property
- Life Sciences
- Materials
- Tech Scout
- Unparalleled Data Quality
- Higher Quality Content
- 60% Fewer Hallucinations
Browse by: Latest US Patents, China's latest patents, Technical Efficacy Thesaurus, Application Domain, Technology Topic, Popular Technical Reports.
© 2025 PatSnap. All rights reserved.Legal|Privacy policy|Modern Slavery Act Transparency Statement|Sitemap|About US| Contact US: help@patsnap.com