Calibration device and method for loading position of mining area driverless system
An unmanned driving and calibration device technology, applied in radio wave measurement systems, satellite radio beacon positioning systems, measurement devices, etc., to achieve the effects of improving calibration accuracy and speed, reducing difficulty and improving efficiency
- Summary
- Abstract
- Description
- Claims
- Application Information
AI Technical Summary
Problems solved by technology
Method used
Image
Examples
Embodiment Construction
[0062] Since the working efficiency of unmanned mining vehicles is higher than that of manual labor, there are higher requirements for the calibration speed and calibration accuracy of the loading position, and the calibration of the loading position requires accurate measurement of the bucket position of the loading equipment. At present, there are some methods for estimating the position of the bucket, including calculating the position of the bucket through the measurement of the hydraulic drive device or the change of the inclination angle, but these methods all have the defect of low calculation accuracy. At the same time, the above method needs to install many sensors. On the one hand, the installation of many sensors means the increase of cost and the complexity of sensor calibration; on the other hand, the installation of many sensors means the increase of cost and also Increase the complexity of sensor calibration; on the other hand, a large number of measurement senso...
PUM
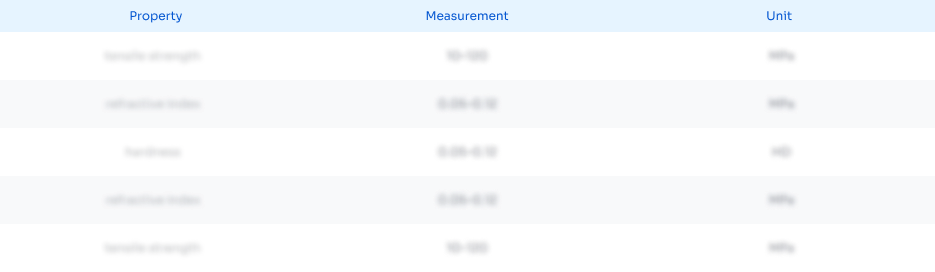
Abstract
Description
Claims
Application Information

- R&D
- Intellectual Property
- Life Sciences
- Materials
- Tech Scout
- Unparalleled Data Quality
- Higher Quality Content
- 60% Fewer Hallucinations
Browse by: Latest US Patents, China's latest patents, Technical Efficacy Thesaurus, Application Domain, Technology Topic, Popular Technical Reports.
© 2025 PatSnap. All rights reserved.Legal|Privacy policy|Modern Slavery Act Transparency Statement|Sitemap|About US| Contact US: help@patsnap.com