Hydraulic roller coating device with accurate coating thickness
A hydraulic and roller coating technology, which is applied to the surface coating liquid device, coating, etc., can solve the problems of high technical and experience requirements for operators, difficulty in improving production efficiency, and unstable coating thickness.
- Summary
- Abstract
- Description
- Claims
- Application Information
AI Technical Summary
Problems solved by technology
Method used
Image
Examples
Embodiment Construction
[0016] Such as figure 1 The precision coating thickness hydraulic roller coating device shown, the roller coating device includes a frame 1, and the front coating roller 23 and the back coating roller 18 are symmetrically arranged on the frame 1, and the front coating roller 23 and the back coating roller The application rollers 18 are located on both sides of the color-coated base plate 35 respectively, so as to realize the monitoring of the coating thickness on the two surfaces of the color-coated base plate 35 . The front dipping roller 25 and the back dipping roller 16 are also symmetrically arranged on the frame 1. The front dipping roller 25 and the front coating roller 23 correspond to each other to form a pair of coating dipping rollers. The back dipping roller 16 Corresponding to the back application roller 18, another pair of application stick rollers is formed. The color-coated base plate 35 is located on the symmetrical plane of the above-mentioned two coating and...
PUM
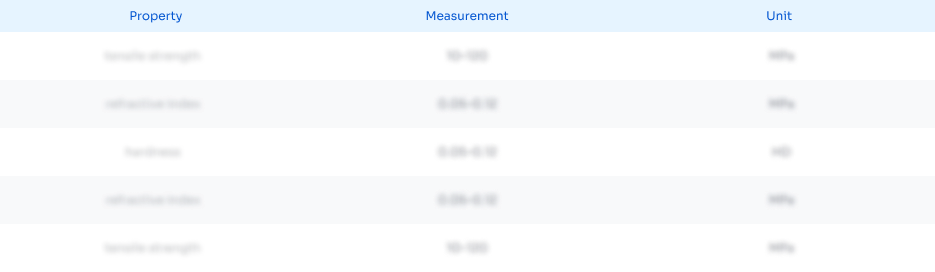
Abstract
Description
Claims
Application Information

- R&D Engineer
- R&D Manager
- IP Professional
- Industry Leading Data Capabilities
- Powerful AI technology
- Patent DNA Extraction
Browse by: Latest US Patents, China's latest patents, Technical Efficacy Thesaurus, Application Domain, Technology Topic, Popular Technical Reports.
© 2024 PatSnap. All rights reserved.Legal|Privacy policy|Modern Slavery Act Transparency Statement|Sitemap|About US| Contact US: help@patsnap.com