Mandrel for manufacturing solid rocket engine and forming method of mandrel
A technology for solid rockets and motors, applied in the field of mandrels for manufacturing solid rocket motors and their molding, which can solve the problems of limited life and high cost of sand mandrels, and achieve the effects of small mass, easy operation, and reduced input costs
- Summary
- Abstract
- Description
- Claims
- Application Information
AI Technical Summary
Problems solved by technology
Method used
Image
Examples
Embodiment 1
[0023] Cut the required glass fiber cloth according to the size of the mandrel, and spray silane coupling agent on the glass fiber cloth, such as KH550, KH560, KH570, etc. Weigh methyl vinyl silicone rubber and carbon black at a weight ratio of 10:1, stir evenly, add curing agent, such as dicumyl hydrogen peroxide, and evenly scrape the silicone rubber after adding dicumyl hydrogen peroxide On the surface of the inner wall of the female mold, the glass fiber cloth sprayed with silane coupling agent is closely attached to the inner surface of the mold after the silicone rubber is scraped to obtain a structure in which a layer of glass fiber cloth and a layer of silicone rubber are bonded. The next layer of glue can be applied until the structure of two layers of glass fiber cloth and three layers of silicone rubber interlaced is formed. Finally, the female mold and tooling are spliced and assembled.
[0024] The main body of the glass fiber cloth is subjected to a tensile te...
Embodiment 2
[0033] Cut the required silicone rubber cloth according to the size of the mandrel, and spray the silane coupling agent on the silicone rubber cloth. Weigh methyl vinyl silicone rubber and carbon black at a weight ratio of 10:1, stir evenly, add dicumyl hydrogen peroxide, and evenly scrape the silicone rubber after adding dicumyl hydrogen peroxide on the inner wall of the female mold On the surface, the silicone rubber cloth sprayed with silane coupling agent is closely attached to the inner surface of the mold after scraping the silicone rubber, and after a layer of silicone rubber cloth and a layer of silicone rubber layer are bonded, the next step can be started. One layer of glue is applied until the structure of two layers of silicone rubber cloth and three layers of silicone rubber layers is formed, and finally the mold and tooling are spliced and assembled.
[0034] The main body of the silicone rubber cloth is subjected to a tensile test, and the shear strength test ...
Embodiment 3
[0043] Cut the required aramid cloth according to the size of the mandrel, and spray the silane coupling agent on the aramid cloth. Weigh methyl vinyl silicone rubber and carbon black at a weight ratio of 10:1, stir evenly, add dicumyl hydrogen peroxide, and evenly scrape the silicone rubber after adding dicumyl hydrogen peroxide on the inner wall of the female mold On the surface, the aramid cloth sprayed with silane coupling agent is closely attached to the inner surface of the mold after the silicone rubber is scraped to form a structure in which a layer of aramid cloth and a layer of silicone rubber are bonded, and then the next step can be started. One layer of glue is applied until a structure of two layers of aramid cloth and three layers of silicone rubber is formed, and finally the mold and tooling are spliced and assembled.
[0044] The tensile test of the aramid cloth body and the shear strength test of the shear sample of the interlaced bonding structure of two l...
PUM
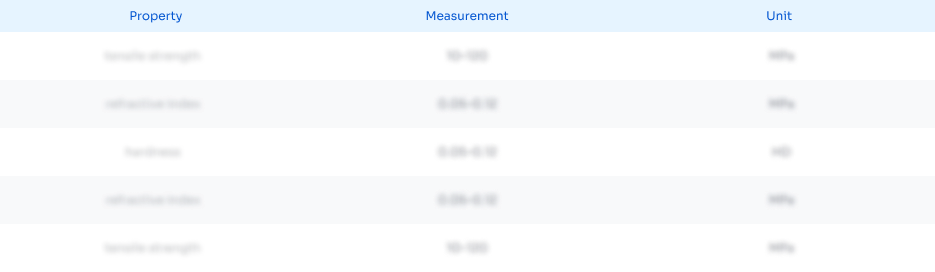
Abstract
Description
Claims
Application Information

- R&D
- Intellectual Property
- Life Sciences
- Materials
- Tech Scout
- Unparalleled Data Quality
- Higher Quality Content
- 60% Fewer Hallucinations
Browse by: Latest US Patents, China's latest patents, Technical Efficacy Thesaurus, Application Domain, Technology Topic, Popular Technical Reports.
© 2025 PatSnap. All rights reserved.Legal|Privacy policy|Modern Slavery Act Transparency Statement|Sitemap|About US| Contact US: help@patsnap.com