Plate hoisting frame structure for automobile punch production line
A production line and lifting frame technology, applied to metal processing equipment, feeding devices, manufacturing tools, etc., can solve problems such as high configuration costs and limited robot motion trajectory, so as to achieve smooth lifting motion, save equipment investment costs, and avoid delays The effect of insufficient tension
- Summary
- Abstract
- Description
- Claims
- Application Information
AI Technical Summary
Problems solved by technology
Method used
Image
Examples
Embodiment Construction
[0008] For better understanding and implementation, the present invention will be further described below in conjunction with accompanying drawing: a kind of sheet material lifting frame structure for stamping production line of automobile, comprises frame 4, is respectively provided with guide post 1, transition wheel 2, The transmission mechanism 3, the tensioning seat 11, etc., the lifting foot 8 is sleeved on the guide column 1 through a linear bearing, and the tensioning wheel 10 is pressed and sleeved on the tensioning seat 11 with screws. It is characterized in that the upper part of the lifting foot 8 is provided with a pull rod Seat 7, the bottom is provided with reaction wheel mechanism 9; Described pull rod seat 7 is provided with the pull rod cover 6 that connects with it with nut; Described pull rod cover 6 is provided with pin 5.
[0009] The chain passes through the transition wheel 2, and one end is worn on the pull rod sleeve 6 with the pin 5, and the other end...
PUM
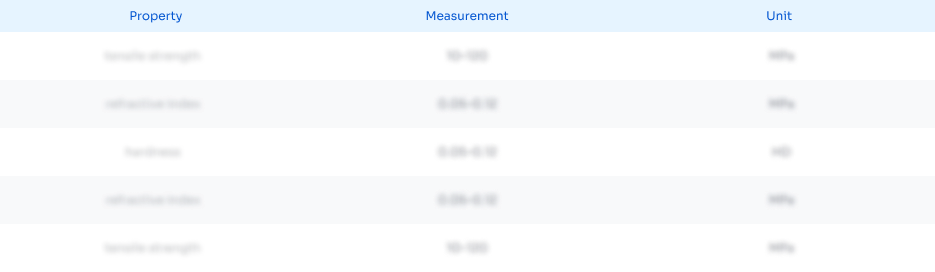
Abstract
Description
Claims
Application Information

- R&D Engineer
- R&D Manager
- IP Professional
- Industry Leading Data Capabilities
- Powerful AI technology
- Patent DNA Extraction
Browse by: Latest US Patents, China's latest patents, Technical Efficacy Thesaurus, Application Domain, Technology Topic, Popular Technical Reports.
© 2024 PatSnap. All rights reserved.Legal|Privacy policy|Modern Slavery Act Transparency Statement|Sitemap|About US| Contact US: help@patsnap.com