Rolled part temperature obtaining method and device for plate-strip hot-rolling production line
An acquisition method and production line technology, applied in the field of hot-rolled strips, can solve the problems of inability to quickly and easily adapt to engineering calculation requirements, poor universality of temperature models, and low calculation accuracy.
- Summary
- Abstract
- Description
- Claims
- Application Information
AI Technical Summary
Problems solved by technology
Method used
Image
Examples
Embodiment 2
[0195] In this embodiment, the ESP production line is taken as an example. On the basis of the method described in Example 1, the temperature of the rolled piece in the production process of the ESP production line is calculated, and compared with the actual temperature value on site, to further illustrate the versatility and accuracy of the method of the present invention. sex.
[0196] The ESP process is a thin slab continuous casting and rolling process. The main equipment layout of the rolling section is as follows: Figure 4 As shown, it includes the first heat preservation cover 1, the three-stand rough rolling unit 2, the second heat preservation cover 3, the induction heating furnace 4, the high-pressure water descaling device 5, the five-stand finishing rolling unit 6, and the laminar flow cooling device 7 And coiler 8, the main equipment spacing is: L1=3m, L2=5m, L3=9.5m, L4=14m, L5=26.5m, L6=37m, L7=45.5m, L8=56m, L9=57m , L10=58m, L11=63m, L12=67.5m, L13=72m, L14=...
Embodiment 3
[0212] Such as Figure 8 The device for obtaining the temperature of a rolled piece in a strip hot rolling production line includes:
[0213] The production line construction unit is used to construct the equipment layout of the hot rolling production line and obtain relevant process parameters;
[0214] The heat exchange area division unit is used to divide the heat exchange area of the rolled piece according to the equipment layout on the production line;
[0215] The grid node division unit is used to divide the grid nodes of the width-thickness section of the rolled piece, and establish the coordinate system parameters and temperature calculation model of each node;
[0216] The initial temperature acquisition unit is used to acquire the initial temperature distribution of the rolled piece at the initial calculation position;
[0217] The heat exchange area judgment and calculation unit is used to judge the heat exchange area where the section of the rolled piece is lo...
PUM
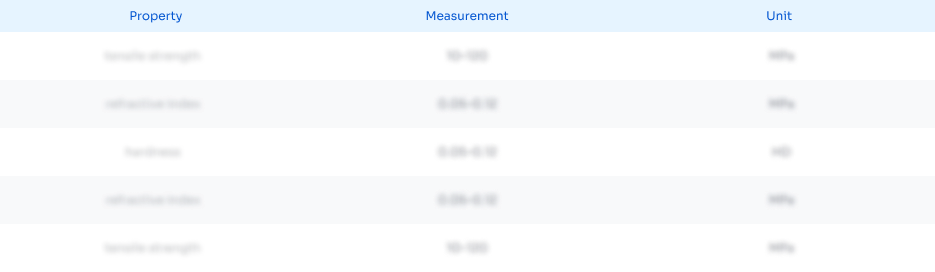
Abstract
Description
Claims
Application Information

- Generate Ideas
- Intellectual Property
- Life Sciences
- Materials
- Tech Scout
- Unparalleled Data Quality
- Higher Quality Content
- 60% Fewer Hallucinations
Browse by: Latest US Patents, China's latest patents, Technical Efficacy Thesaurus, Application Domain, Technology Topic, Popular Technical Reports.
© 2025 PatSnap. All rights reserved.Legal|Privacy policy|Modern Slavery Act Transparency Statement|Sitemap|About US| Contact US: help@patsnap.com