Method for removing deteriorated layer on stainless steel surface
A surface metamorphic layer and stainless steel technology, applied in the field of polishing, can solve the problems of uneven brightness, damage to the surface flatness and precision of parts, and the inability to guarantee the flatness of parts, etc., and achieve the effect of good surface finish and bright color
- Summary
- Abstract
- Description
- Claims
- Application Information
AI Technical Summary
Problems solved by technology
Method used
Image
Examples
Embodiment 1
[0044] (1) The preparation ratio (by weight) of the polishing liquid raw material additive: salt solution: water=1:10:180; The salt solution is ammonium sulfate and potassium chloride, and the ratio is 4:1; The additive contains 30% phosphoric acid, 60 % organic acid acetic acid, 10% complexing agent EDTMPS, obtain electrolyte plasma polishing fluid;
[0045] (2) Pour the prepared and evenly stirred electrolyte plasma polishing liquid into the polishing tank, and heat the polishing liquid to 70°C;
[0046] (3) According to the structural size of the 316L stainless steel parts, the polishing fixture and the pendant are used, and the 316L stainless steel parts with a metamorphic layer after the hot isostatic pressing are installed on the polishing pendant. Put the polishing fixture and the parts on the pendant into the above polishing tank, and completely immerse the parts in the polishing solution. The fixture and parts are connected to the positive pole of the power supply, an...
Embodiment 2
[0050] (1) The preparation ratio (by weight) of polishing fluid raw materials Additives: salt solution: water = 1:7:170; the salt solution is ammonium sulfate and barium chloride, the ratio is 4:1; the additive contains 40% phosphoric acid, 40 % organic acid acetic acid, 10% sodium gluconate, 10% complexing agent EDTMPS;
[0051] (2) Pour the prepared and evenly stirred electrolyte plasma polishing solution into the polishing tank until the temperature of the polishing solution is 75°C;
[0052] (3) Put the polishing fixture and parts on the pendant into the above polishing tank, and completely immerse the parts in the polishing solution; the fixture and parts are connected to the positive pole of the power supply, and the polishing tank is connected to the negative pole of the power supply, and the output voltage is controlled at 330V;
[0053] (4) The 316L stainless steel parts that produce a metamorphic layer after the hot isostatic pressing process are subjected to plasma ...
Embodiment 3
[0056] (1) The preparation ratio (by weight) of polishing fluid raw materials Additives: salt solution: water=1:8:200; salt solution contains 80% ammonium sulfate, 10% potassium chloride, 10% barium chloride; additive contains 50% % phosphoric acid, 30% organic acid acetic acid, 5% sodium gluconate, 15% complexing agent EDTMPS;
[0057] (2) Pour the prepared and evenly stirred electrolyte plasma polishing solution into the polishing tank until the temperature of the polishing solution is 80°C;
[0058] (3) Put the polishing fixture and parts on the pendant into the above polishing tank, and completely immerse the parts in the polishing solution; the fixture and parts are connected to the positive pole of the power supply, and the polishing tank is connected to the negative pole of the power supply, and the output voltage is controlled at 300V;
[0059] (4) The 316L stainless steel parts that produce a metamorphic layer after the hot isostatic pressing process are subjected to ...
PUM
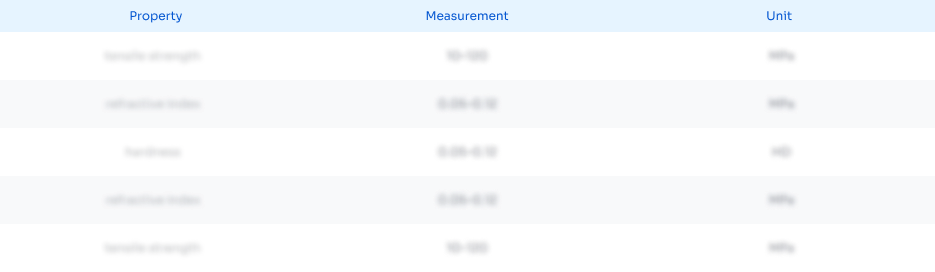
Abstract
Description
Claims
Application Information

- Generate Ideas
- Intellectual Property
- Life Sciences
- Materials
- Tech Scout
- Unparalleled Data Quality
- Higher Quality Content
- 60% Fewer Hallucinations
Browse by: Latest US Patents, China's latest patents, Technical Efficacy Thesaurus, Application Domain, Technology Topic, Popular Technical Reports.
© 2025 PatSnap. All rights reserved.Legal|Privacy policy|Modern Slavery Act Transparency Statement|Sitemap|About US| Contact US: help@patsnap.com