Preparation method of diphenyl cyclosiloxane
A technology of diphenylcyclosiloxane and diphenyldimethoxysilane is applied in the field of preparation of organosilicon intermediates, and can solve the problems of high cost, difficulty, and Pn quality of diphenylsiloxane. , to achieve the effect of avoiding VOCs emission, small thermal effect and low energy consumption
- Summary
- Abstract
- Description
- Claims
- Application Information
AI Technical Summary
Problems solved by technology
Method used
Image
Examples
Embodiment 1
[0051] Add 120g of diethylene glycol dimethyl ether, 14g of water, and 2g of tetramethylammonium hydroxide (TMAOH) aqueous solution to the bottle, wherein the concentration of tetramethylammonium hydroxide aqueous solution is 1mol / L, and the kettle liquid is preheated to 95~ At 100°C, there is a slight reflux state on the bottle wall. Raise the temperature of the glass rectification column to 60°C and keep it. Slowly add 120g of diphenyldimethoxysilane with the total amount of treated PCBs less than 0.5ppm and the total amount of phenyltrimethoxysilane less than 0.5ppm into the bottle, adjust the heating according to the temperature of the kettle liquid, and keep the temperature of the kettle liquid At 95-100°C. From the beginning of the dropwise addition, the kettle liquid began to become turbid in about 1 hour. After 2 hours of dropwise addition, the methanol distilled from the top of the column was collected from the receiving bottle. This methanol only contains part of th...
Embodiment 2
[0055] Embodiment 2: 1: (0.06~0.2): (0.001~0.002)
[0056] Add 120g of diethylene glycol diethyl ether, 8g of water, and 1.2g of tetramethylammonium hydroxide (TMAOH) aqueous solution to the bottle, wherein the concentration of tetramethylammonium hydroxide aqueous solution is 1mol / L, and preheat the kettle liquid to 98°C , There is a slight reflux state on the bottle wall. Similarly, raise the temperature of the glass rectification column to 60°C and keep it. Slowly add 130g of diphenyldimethoxysilane with the total amount of treated PCBs less than 0.5ppm and the total amount of phenyltrimethoxysilane less than 0.5ppm into the bottle, adjust the heating according to the temperature of the kettle liquid, and keep the temperature of the kettle liquid At 95-100°C. From the beginning of the dropwise addition, the kettle liquid began to become turbid in about 1 hour, and was added dropwise for 2 hours.
[0057] The remaining processing steps were the same as in Example 1, and t...
Embodiment 3
[0059] Add 120g of ethylene glycol diethyl ether, 20g of water, and 2.3g of tetramethylammonium hydroxide (TMAOH) aqueous solution to the bottle, wherein the concentration of tetramethylammonium hydroxide aqueous solution is 1mol / L, and the kettle liquid is preheated to 99°C. There is a slight reflux state on the bottle wall. Similarly, raise the temperature of the glass rectification column to 60°C and keep it. Slowly add 115g of diphenyldimethoxysilane with the total amount of treated PCBs less than 0.5ppm and the total amount of phenyltrimethoxysilane less than 0.5ppm into the bottle, adjust the heating according to the temperature of the kettle liquid, and keep the temperature of the kettle liquid At 95-100°C. From the beginning of the dropwise addition, the kettle liquid began to become turbid in about 1 hour, and was added dropwise for 2 hours.
[0060] The remaining processing steps were the same as in Example 1, and finally the powder was dried under reduced pressure...
PUM
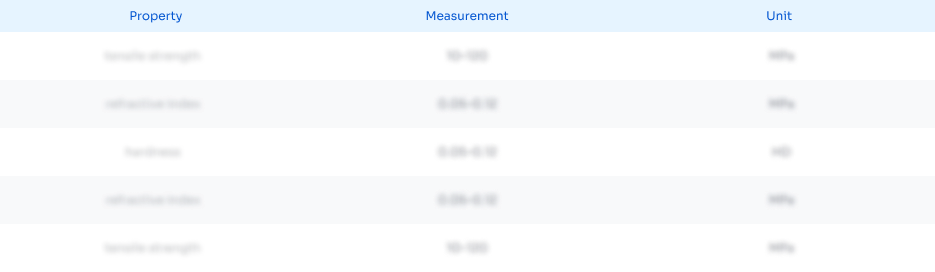
Abstract
Description
Claims
Application Information

- R&D Engineer
- R&D Manager
- IP Professional
- Industry Leading Data Capabilities
- Powerful AI technology
- Patent DNA Extraction
Browse by: Latest US Patents, China's latest patents, Technical Efficacy Thesaurus, Application Domain, Technology Topic, Popular Technical Reports.
© 2024 PatSnap. All rights reserved.Legal|Privacy policy|Modern Slavery Act Transparency Statement|Sitemap|About US| Contact US: help@patsnap.com