Laser cladding powder presetting method
A laser cladding and powder technology, applied in the direction of metal material coating process, coating, etc., can solve the problems of cladding powder splash and other problems, and achieve the effect of uniform thickness, smooth surface and good cladding effect.
- Summary
- Abstract
- Description
- Claims
- Application Information
AI Technical Summary
Problems solved by technology
Method used
Image
Examples
Embodiment 1
[0035] First, pre-treat the surface of the substrate to be clad, clean the surface of dust, oil or rust, and dry to obtain a clean and dry substrate surface;
[0036] Then, the substrate to be clad is fixed on the sample holder, and the cladding powder is evenly paved on the surface of the substrate (powder composition: Fe 70wt%, Mo 2wt%, B 5wt%, Cr 4wt%, W 8wt%, Ni 3wt%, Si 5wt%, Mn 3wt%);
[0037] Then, the chemical glue is evenly sprayed onto the surface of the cladding powder, and the spraying amount is 4wt% of the cladding powder;
[0038] Finally, a semiconductor coupled laser is used for laser cladding operation, and an argon protective atmosphere is used during cladding; the process parameters used for laser cladding in this embodiment are: laser power 1500W, spot diameter 5mm, and cladding speed 350mm / min.
Embodiment 2
[0040] First, pre-treat the surface of the substrate to be clad, clean the surface of dust, oil or rust, and dry to obtain a clean and dry substrate surface;
[0041] Then, the substrate to be clad is fixed on the sample holder, and the cladding powder is evenly paved on the surface of the substrate (powder composition: Co 38.5wt%, Ni 32wt%, Cr 21wt%, Al 8wt%, Y0.5wt% %);
[0042] Then, the chemical glue is evenly sprayed onto the surface of the cladding powder, and the spraying amount is 4wt% of the cladding powder;
[0043] Finally, a semiconductor coupled laser is used for laser cladding, and an argon protective atmosphere is used during cladding; the process parameters used for laser cladding in this embodiment are: laser power 1500W, spot diameter 5mm, and cladding speed 300mm / min.
Embodiment 3
[0045] First, pre-treat the surface of the substrate to be clad, clean the surface of dust, oil or rust, and dry to obtain a clean and dry substrate surface;
[0046] Then, the substrate to be clad is fixed on the sample holder, and the cladding powder is evenly paved on the surface of the substrate (powder composition: Fe 70wt%, Mo 2wt%, B 5wt%, Cr 4wt%, W 8wt%, Ni 3wt%, Si 5wt%, Mn 3wt%);
[0047] Then, the chemical glue is evenly sprayed onto the surface of the cladding powder, and the spraying amount is 8wt% of the cladding powder;
[0048] Finally, a semiconductor coupled laser is used for laser cladding operation, and an argon protective atmosphere is used during cladding; the process parameters used for laser cladding in this embodiment are: laser power 1500W, spot diameter 5mm, and cladding speed 350mm / min.
PUM
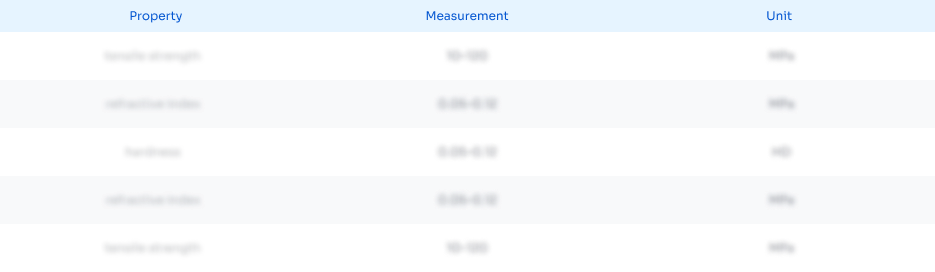
Abstract
Description
Claims
Application Information

- R&D
- Intellectual Property
- Life Sciences
- Materials
- Tech Scout
- Unparalleled Data Quality
- Higher Quality Content
- 60% Fewer Hallucinations
Browse by: Latest US Patents, China's latest patents, Technical Efficacy Thesaurus, Application Domain, Technology Topic, Popular Technical Reports.
© 2025 PatSnap. All rights reserved.Legal|Privacy policy|Modern Slavery Act Transparency Statement|Sitemap|About US| Contact US: help@patsnap.com