Preparation method of seepage-proof castable
A castable and anti-seepage agent technology, applied in the field of refractory materials, can solve the problems of furnace lining damage, poor wettability of aluminum liquid, easy to pollute the composition of aluminum liquid, etc. Effect of non-wetting by molten aluminum
- Summary
- Abstract
- Description
- Claims
- Application Information
AI Technical Summary
Problems solved by technology
Method used
Examples
Embodiment 1
[0013] Example 1: An anti-seepage castable is composed of 8mm-0mm bauxite particles 69wt%, 4 0.4wt%, TiB 2 0.2wt%, SrTiO 3 0.2wt%, Na3AlF6 0.2wt%); and add 0.12% sodium tripolyphosphate and 0.03% polycarboxylate as dispersants in the total weight of raw materials; when preparing, firstly mix anti-seepage agent and nitrogen with particle size <0.044mm The aluminum fine powder raw material is co-milled in a vibration mill for 30mins; the anti-seepage agent and aluminum nitride fine powder are fully homogenized in advance to make homogenized powder, and then the homogenized powder is mixed with anti-seepage agent and aluminum nitride fine powder in nitrogen The total proportion of aluminum refractory castables is 22wt%, mixed with other components evenly, and about 5wt% aluminum sol is added during construction and stirring, mixed evenly, vibrating poured at the furnace site, and used after conventional curing and baking.
Embodiment 2
[0014] Example 2: An anti-seepage castable consists of 8mm-0mm alumina particles 66wt%, 4 1.6wt%, TiB 2 0.8wt%, SrTiO 3 0.8wt%, Na3AlF6 0.8wt%); and add 0.12% sodium tripolyphosphate and 0.03% polycarboxylate as dispersants; the preparation process is the same as in Example 1, and about 6wt% aluminum is added during construction and stirring Colloidal sol, kneaded evenly, vibrating poured on the furnace site, used after conventional curing and baking.
Embodiment 3
[0015] Example 3: An anti-seepage castable consists of 8mm-0mm alumina particles 65wt%, 4 1.6wt%, TiB 2 0.8wt%, SrTiO 3 0.8wt%, Na 3 AlF 6 0.8wt%); and add 0.12% sodium tripolyphosphate and 0.03% polycarboxylate as dispersant in the total weight of raw materials; the preparation process is the same as in Example 1, and about 8wt% aluminum sol is added during construction and stirring, and the mixing is uniform , vibrated pouring at the furnace site, and used after conventional curing and baking.
PUM
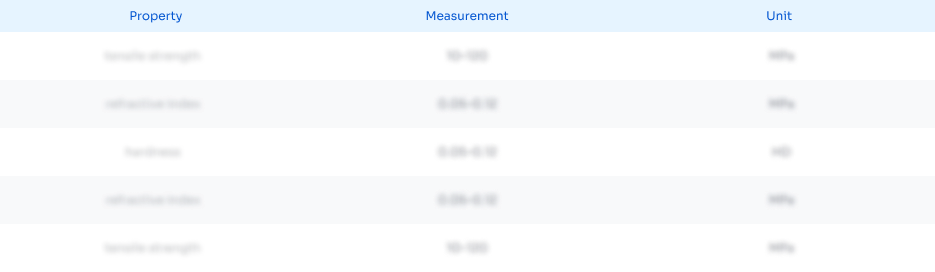
Abstract
Description
Claims
Application Information

- R&D
- Intellectual Property
- Life Sciences
- Materials
- Tech Scout
- Unparalleled Data Quality
- Higher Quality Content
- 60% Fewer Hallucinations
Browse by: Latest US Patents, China's latest patents, Technical Efficacy Thesaurus, Application Domain, Technology Topic, Popular Technical Reports.
© 2025 PatSnap. All rights reserved.Legal|Privacy policy|Modern Slavery Act Transparency Statement|Sitemap|About US| Contact US: help@patsnap.com