An anti-warping structure for injection molded parts
A technology of anti-warping and injection molded parts, which is applied in the direction of electrical components, parts of connecting devices, coupling devices, etc., can solve problems such as increasing the size of the mounting surface, unfavorable miniaturization design, and failure of seals, so as to reduce injection molding The effect of reducing the size of the parts, reducing the size of the connector, and reducing the assembly space
- Summary
- Abstract
- Description
- Claims
- Application Information
AI Technical Summary
Problems solved by technology
Method used
Image
Examples
Embodiment Construction
[0019] In order to further illustrate the technical means and technical effects adopted by the present invention, the present invention will be described in detail below in conjunction with the examples.
[0020] The anti-warping structure for the injection molded part 3 of the present invention includes a cross bar 1 and through holes I2 arranged at both ends of the cross bar. The through hole I and the cross bar are integrated. The anti-warping structure is made of stainless steel, which is formed as a whole by stamping, and has the characteristics of high hardness and not easy to bend. The surface of the anti-warping structure can also be coated with a layer of coating, which can be nickel-plated layer or zinc-nickel layer or passivation treatment layer to prevent the anti-warping structure from being exposed to the air for a long time or during use The base material is corroded.
[0021] The injection molded part panel 4 used in conjunction with the anti-warping structure...
PUM
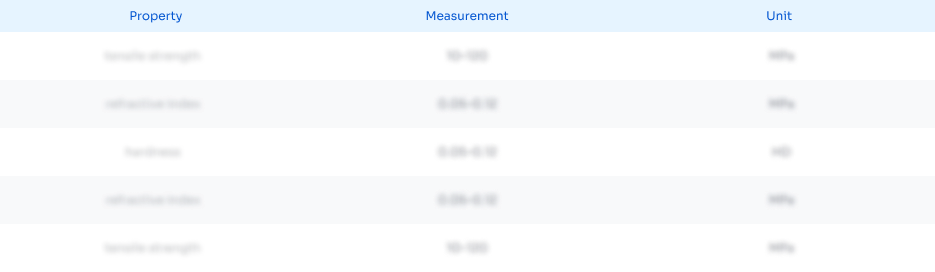
Abstract
Description
Claims
Application Information

- R&D
- Intellectual Property
- Life Sciences
- Materials
- Tech Scout
- Unparalleled Data Quality
- Higher Quality Content
- 60% Fewer Hallucinations
Browse by: Latest US Patents, China's latest patents, Technical Efficacy Thesaurus, Application Domain, Technology Topic, Popular Technical Reports.
© 2025 PatSnap. All rights reserved.Legal|Privacy policy|Modern Slavery Act Transparency Statement|Sitemap|About US| Contact US: help@patsnap.com