Coal gangue powder-based grouting material for pavement voids and preparation method of coal gangue powder-based grouting material
A technology of grouting material and coal gangue powder, which is applied in the field of coal gangue powder-based grouting materials and its preparation, and can solve problems such as ineffective utilization of coal gangue, ecological environment damage, and high bleeding rate
- Summary
- Abstract
- Description
- Claims
- Application Information
AI Technical Summary
Problems solved by technology
Method used
Image
Examples
preparation example Construction
[0035] A method for preparing a coal gangue powder-based grouting material for pavement voiding, comprising the following specific steps:
[0036] The first step, weigh the following raw materials by mass parts, 80-100 parts of coal gangue powder, 40-60 parts of fly ash, 30-60 parts of slag powder, 60-90 parts of water, 200-400 parts of sand, 54 -80 parts of water glass solution, 8-20 parts of KOH solid, 1-2 parts of defoamer, 3-5 parts of expansion agent, 1-2 parts of retarder, 1-2 parts of redispersible latex powder;
[0037] The second step is to prepare liquid B: Weigh the water glass solution and KOH solid, pour the KOH solid into the water glass solution and stir slowly until it is completely dissolved. Since the KOH solid dissolves in the water glass solution, it will release heat, so it needs to be stirred slowly. stir;
[0038] The third step is to prepare the A mixture: Put the weighed coal gangue powder, slag powder, fly ash, sand, defoamer, redispersible latex pow...
Embodiment 1
[0041] Step 1), weigh raw materials by mass parts:
[0042] 80 parts of coal gangue powder, 40 parts of slag powder, 60 parts of fly ash, 70 parts of water, 200 parts of gravel, 55 parts of water glass solution, 8 parts of KOH solid, 1 part of defoamer, 3 parts of expansion agent, retarder 1 part, 1 part of redispersible latex powder;
[0043] Step 2), mix the weighed KOH solid into the water glass solution, stir until the KOH solid is completely dissolved, and obtain B component;
[0044] Step 3), put the weighed coal gangue powder, slag powder, fly ash and sand into the mixer for dry mixing and mixing evenly, so that the powder is fully mixed, and increase the amount of coal gangue powder, slag powder, fly ash and sand Then put coal gangue powder, slag powder, fly ash, sand, defoamer, expansion agent, retarder, and redispersible latex powder into the mixer for 3-5 minutes to make them evenly mixed , to increase the contact area between the components; then put in water and m...
Embodiment 2
[0047] Step 1), weigh raw materials by mass parts:
[0048] 80 parts of coal gangue powder, 60 parts of slag powder, 60 parts of fly ash, 90 parts of water, 200 parts of gravel, 80 parts of water glass solution, 16 parts of KOH solid, 1 part of defoamer, 5 parts of expansion agent, retarder 2 parts, 1 part of redispersible latex powder;
[0049] Step 2), mix the weighed KOH solid into the water glass solution, stir until the KOH solid is completely dissolved, and obtain B component;
[0050] Step 3), put the weighed coal gangue powder, slag powder, fly ash and sand into the mixer for dry mixing and mixing evenly, so that the powder is fully mixed, and increase the amount of coal gangue powder, slag powder, fly ash and sand Then put coal gangue powder, slag powder, fly ash, sand, defoamer, expansion agent, retarder, and redispersible latex powder into the mixer for 3-5 minutes to make them evenly mixed , to increase the contact area between the components; then put in water a...
PUM
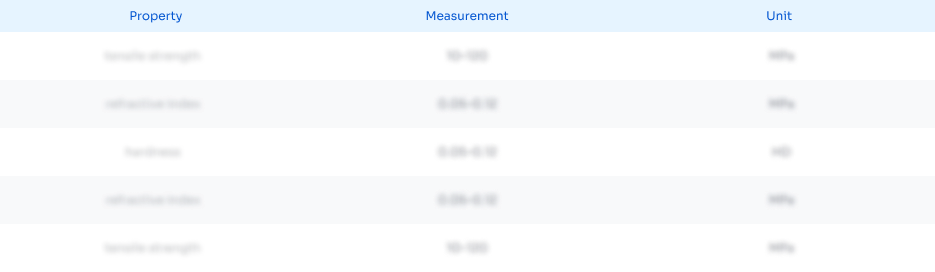
Abstract
Description
Claims
Application Information

- R&D
- Intellectual Property
- Life Sciences
- Materials
- Tech Scout
- Unparalleled Data Quality
- Higher Quality Content
- 60% Fewer Hallucinations
Browse by: Latest US Patents, China's latest patents, Technical Efficacy Thesaurus, Application Domain, Technology Topic, Popular Technical Reports.
© 2025 PatSnap. All rights reserved.Legal|Privacy policy|Modern Slavery Act Transparency Statement|Sitemap|About US| Contact US: help@patsnap.com