Antibacterial flame-retardant fibers and preparation method of fabric of antibacterial flame-retardant fibers
A technology of flame retardant fibers and flame retardant fabrics, applied in the field of preparation of antibacterial and flame retardant fibers, can solve the problems of uneven mixing of flame retardants and antibacterial agents, low moisture regain of polyester fibers, secondary personal injury, etc., and achieve antibacterial resistance. Long-lasting and stable combustion performance, excellent mechanical properties, and the effect of alleviating resource shortages
- Summary
- Abstract
- Description
- Claims
- Application Information
AI Technical Summary
Problems solved by technology
Method used
Image
Examples
preparation example Construction
[0042] The preparation method of a kind of antibacterial flame-retardant fiber that the present invention relates to specifically implements according to the following steps:
[0043] Step 1, collecting the pure white cotton waste textiles, and then washing and drying the collected white pure cotton waste textiles and crushing them;
[0044] Step 2, bleaching the crushed natural white pure cotton waste textiles with hydrogen peroxide, the mass fraction of hydrogen peroxide is 8-12%, the treatment temperature is controlled at 60-90°C, bleaching for 50-80 minutes, and then drying to obtain cellulose raw material;
[0045] Step 3, treating the cellulose raw material obtained in step 2 with 10-20% sodium hydroxide or 45% sodium carbonate solution for 1-3 hours, and drying at a temperature of 80-90° C. to obtain alkali cellulose;
[0046]Step 4, mixing the alkali cellulose prepared in step 3 with the hydroxyl-containing phosphorus flame retardant, and then adding a crosslinking ag...
Embodiment 1
[0061] A method for preparing antibacterial and flame-retardant fibers, specifically implemented according to the following steps:
[0062] Step 1, collecting the pure white cotton waste textiles, and then washing and drying the collected white pure cotton waste textiles and crushing them;
[0063] Step 2, the pulverized material is subjected to oxygen bleaching with hydrogen peroxide, the mass fraction of hydrogen peroxide is 12%, the treatment temperature is controlled at 60° C., bleached for 80 minutes, and dried to obtain cellulose raw material;
[0064] Step 3, treating the cellulose raw material with 10% sodium hydroxide solution for 3 hours, drying at 80°C to obtain alkali cellulose;
[0065] Step 4, mixing alkali cellulose with a certain mass fraction of a hydroxyl-containing phosphorus-based flame retardant, using urea as a crosslinking agent, causing the flame retardant to undergo hydroxylamination crosslinking reaction with the alkali cellulose, and preparing flame-...
Embodiment 2
[0078] A method for preparing antibacterial and flame-retardant fibers, specifically implemented according to the following steps:
[0079] Step 1, collecting the pure white cotton waste textiles, and then washing and drying the collected white pure cotton waste textiles and crushing them;
[0080] Step 2, the pulverized material is subjected to oxygen bleaching with hydrogen peroxide, the mass fraction of hydrogen peroxide is 10%, the treatment temperature is controlled at 70° C., bleached for 60 minutes, and dried to obtain cellulose raw material;
[0081] Step 3, treating the bleached product in step 1 with 20% sodium hydroxide solution for 4 hours, drying at 85°C to obtain alkali cellulose;
[0082] Step 4, mixing the alkali cellulose with a certain mass fraction of a hydroxyl-containing phosphorus flame retardant, using urea as a crosslinking agent, causing the flame retardant to undergo a hydroxylaminated crosslinking reaction with the alkali cellulose to prepare the fla...
PUM
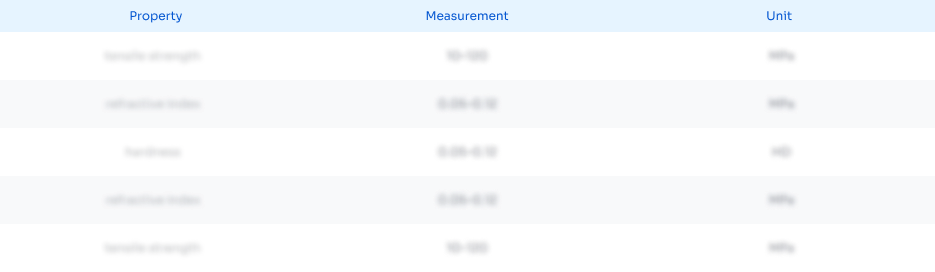
Abstract
Description
Claims
Application Information

- Generate Ideas
- Intellectual Property
- Life Sciences
- Materials
- Tech Scout
- Unparalleled Data Quality
- Higher Quality Content
- 60% Fewer Hallucinations
Browse by: Latest US Patents, China's latest patents, Technical Efficacy Thesaurus, Application Domain, Technology Topic, Popular Technical Reports.
© 2025 PatSnap. All rights reserved.Legal|Privacy policy|Modern Slavery Act Transparency Statement|Sitemap|About US| Contact US: help@patsnap.com