System and method for preparing disilane and propyl silane by silane pyrolysis method
A technology of disilane and trisilane, which is applied in the system field of preparing disilane and trisilane by silane pyrolysis, can solve the problems of difficult device development and low practical value, and achieve easy device, high silane conversion rate and simple process flow Effect
- Summary
- Abstract
- Description
- Claims
- Application Information
AI Technical Summary
Problems solved by technology
Method used
Image
Examples
specific Embodiment 1
[0034] A system for preparing disilane and trisilane by silane pyrolysis, such as figure 1 As shown, it includes feed heater 1, silane pyrolysis reactor 2, heat exchange and compression system 3, hydrogen separator 4, silane rough separator 5, silane separation tower 6, disilane rough separator 7 and B The silane separation tower 8, the gas phase outlet of the hydrogen separator 4, the gas phase outlet of the silane rough separator 5 and the gas phase outlet of the silane separation tower 6 are respectively connected with the shell-side inlet of the heat exchange and compression system 3, and the heat exchange and compression system 3 The shell side outlet is connected to the inlet of the raw material heater 1, the top gas phase outlet of the disilane rough separator 7 and the top gas phase outlet of the disilane separation tower 8 are respectively connected to the external disilane storage tank 9, and the bottom liquid phase of the disilane separation tower 8 The outlet is co...
specific Embodiment 2
[0038] A kind of method that utilizes above-mentioned specific embodiment one system to carry out silane pyrolysis to prepare disilane and trisilane, comprises the following steps:
[0039] (1) will be made by H 2 and SiH 4 The raw materials of the composition are sent to the raw material heater 1 for preheating, and then sent to the silane pyrolysis reactor 2, and the reaction temperature in the silane pyrolysis reactor 2 is controlled to be 470°C-550°C, and the pressure is controlled to be 0.6-1.3MPaG, After reacting for 5-30s, the mixed gas obtained by silane pyrolysis is sent to the heat exchange and compression system 3 for cooling, and then sent to the hydrogen separator 4, wherein the 2 and SiH 4 The concentration of silane in the raw materials is 20-35% mol, and the wall of the silane pyrolysis reactor 2 adopts a jacket structure containing heat transfer oil, and the temperature of the wall is controlled at 50-150°C;
[0040] (2) Control the temperature in the hydro...
Embodiment 1
[0048] According to the design scale of disilane product is 72t / a (the product is calculated as disilane, the annual operation time is 7200h), the reaction temperature in silane pyrolysis reactor 2 is 500℃, and the reaction pressure is 0.9MPaG. The one-way conversion rate of silane is 5%, and the residence time is 10s, which is obtained by H 2 and SiH 4 The silane concentration in the starting material was 25% mol. The pressure in the hydrogen separator 4 is controlled at 0.9 MPaG, and the temperature is controlled at -120°C. The pressure of the silane rough separator 5 is 0.2MPaG, and the temperature is -80°C. The temperature of the disilane rough separator 7 is -40°C, and the pressure is 0.15MPaG. After the system reaction is balanced, the fresh feed of silane per hour is 0.4054kmol / h, the output of disilane is 0.161kmol / h (about 10kg / h), and the output of trisilane is 0.0278kmol / h (about 2.5kg / h) , and H needs to be vented every hour 2 0.21Kmol / h. The reaction equati...
PUM
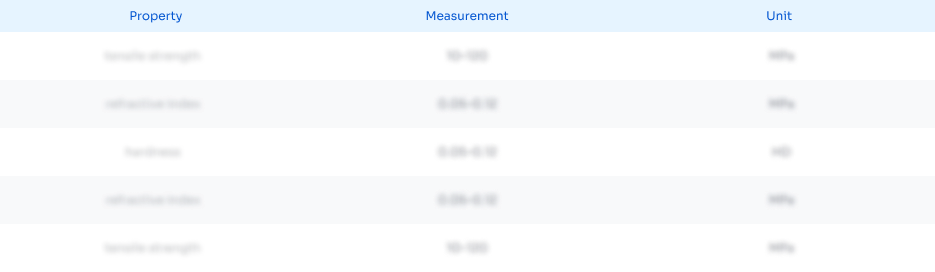
Abstract
Description
Claims
Application Information

- R&D
- Intellectual Property
- Life Sciences
- Materials
- Tech Scout
- Unparalleled Data Quality
- Higher Quality Content
- 60% Fewer Hallucinations
Browse by: Latest US Patents, China's latest patents, Technical Efficacy Thesaurus, Application Domain, Technology Topic, Popular Technical Reports.
© 2025 PatSnap. All rights reserved.Legal|Privacy policy|Modern Slavery Act Transparency Statement|Sitemap|About US| Contact US: help@patsnap.com