Automatic fuel cell stacking system
A technology of fuel cells and electric stacks, applied in the field of fuel cell automatic stacking systems, which can solve problems such as difficult to control the balance of fastening, damage to proton exchange membrane fuel cells, and increased contact resistance
- Summary
- Abstract
- Description
- Claims
- Application Information
AI Technical Summary
Problems solved by technology
Method used
Image
Examples
Embodiment Construction
[0028] The following are specific embodiments of the present invention and in conjunction with the accompanying drawings, the technical solutions of the present invention are further described, but the present invention is not limited to these embodiments.
[0029] Such as figure 1 As shown, an automatic fuel cell stacking system of the present invention includes a transfer and conveying device 2, a stack assembly device 7, a press-fit locking device 5 and a detection device 1; the stack assembly device 7 is used to stack electrodes The plates are stacked to form a stack assembly module 11, the press-fit locking device 5 is used to press-fit and lock the stack assembly module 11, and the detection device 1 is used to test the airtightness and insulation of the stack assembly module 11; The loading and conveying device 2 includes a conveying mechanism 20 and a plurality of transfer mechanisms 30. The cell stack stacking device 7, the press-fit locking device 5 and the detection...
PUM
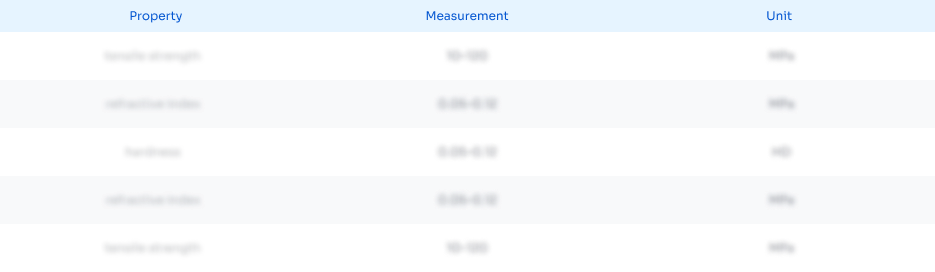
Abstract
Description
Claims
Application Information

- R&D
- Intellectual Property
- Life Sciences
- Materials
- Tech Scout
- Unparalleled Data Quality
- Higher Quality Content
- 60% Fewer Hallucinations
Browse by: Latest US Patents, China's latest patents, Technical Efficacy Thesaurus, Application Domain, Technology Topic, Popular Technical Reports.
© 2025 PatSnap. All rights reserved.Legal|Privacy policy|Modern Slavery Act Transparency Statement|Sitemap|About US| Contact US: help@patsnap.com