A process for synergistically producing calcium aluminate powder using power station boilers
A power plant boiler and calcium aluminate powder technology, which is applied in the preparation of calcium aluminate, alkaline earth metal aluminate/aluminum oxide/aluminum hydroxide, chemical industry, etc., can solve the problem of unstable temperature field of rotary kiln and long product production cycle , over-burning or under-burning of raw materials, etc., to achieve the effects of stable production process parameters, improved energy utilization efficiency, and fast response speed
- Summary
- Abstract
- Description
- Claims
- Application Information
AI Technical Summary
Problems solved by technology
Method used
Image
Examples
Embodiment 1
[0023] Example 1 (using pulverized coal boiler)
[0024] A process for producing calcium aluminate powder by utilizing a power station boiler, comprising the following steps:
[0025] (1) Using a microcomputer batching device to prepare raw materials, the raw materials include the following components by weight: 50% to 70% of coal, 10% to 20% of calcium oxide, 20% to 30% of alumina, and iron oxide (accounting for than 1%);
[0026] (2) After the raw materials are mixed, they are conveyed to the crusher (pulverizer) by the belt for crushing and pulverizing;
[0027] (3) The crushed powder materials are sent to the storage bin (homogenization bin) through the material conveyor;
[0028] (4) The material is controlled by the powder selection screen of the pulverizing device to control the particle size of the material to be 500~1000 mesh, and sent to the pulverized coal boiler through the boiler feeding device for combustion, and the temperature is controlled at 1200~1300 ℃;
...
Embodiment 2
[0031] Example 2 (using a fluidized bed boiler)
[0032] A process for producing calcium aluminate powder by utilizing a power station boiler, comprising the following steps:
[0033] (1) Using a microcomputer batching device to configure raw materials, the raw materials include the following components by weight: 50% to 70% of coal, 10% to 20% of calcium oxide, 20% to 30% of alumina, and gypsum (the proportion of 1%);
[0034] (2) After the raw materials are mixed, they are conveyed to the crusher (pulverizer) by the belt for crushing and pulverizing;
[0035] (3) The crushed powder materials are sent to the storage bin (homogenization bin) through the material conveyor;
[0036] (4) The material is controlled by the crusher screen to control the particle size of the material to be 0~13mm, and sent to the fluidized bed for combustion through the boiler feeding device, and the temperature is controlled at 850~1050℃;
[0037] (5) The fly ash after combustion is collected by ...
PUM
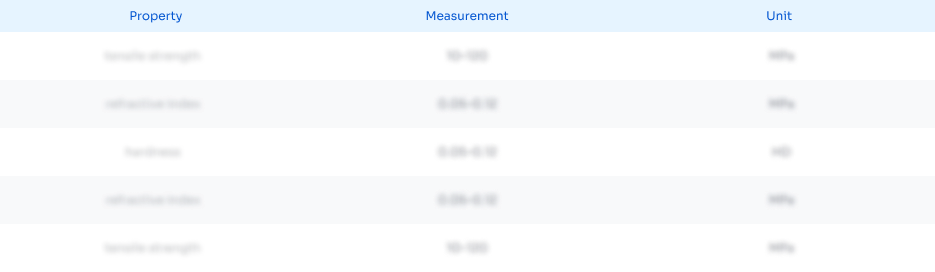
Abstract
Description
Claims
Application Information

- R&D
- Intellectual Property
- Life Sciences
- Materials
- Tech Scout
- Unparalleled Data Quality
- Higher Quality Content
- 60% Fewer Hallucinations
Browse by: Latest US Patents, China's latest patents, Technical Efficacy Thesaurus, Application Domain, Technology Topic, Popular Technical Reports.
© 2025 PatSnap. All rights reserved.Legal|Privacy policy|Modern Slavery Act Transparency Statement|Sitemap|About US| Contact US: help@patsnap.com