Bilateral thin-wall barrel port inward curling machine
A crimping machine and thin-walled technology, applied in the field of machinery and equipment, can solve the problems of low production efficiency, poor machining accuracy, and inability to mass-produce, and achieve the effects of reducing manpower usage, improving symmetry accuracy, and improving automation rate.
- Summary
- Abstract
- Description
- Claims
- Application Information
AI Technical Summary
Problems solved by technology
Method used
Image
Examples
Embodiment 1
[0052] Such as figure 1 As shown, this application adopts a main body mechanism with relative movement of tooling boxes 3 on both sides of a reference working surface. The first motor 1 is installed on the left side of the application, and the first motor 1 is a servo motor; the first reducer 2 is installed On the right side of the first motor 1, the first reducer 2 is a planetary reducer; the hexagonal drive shaft is connected to the output hole of the first reducer 2 and runs through the bottom of the tooling box 3 on both sides, and the tooling box 3 on both sides Two sprockets 6 are arranged on the hexagonal transmission shaft at the bottom, and the sprocket 6 is fixedly connected with the bottom of the tooling box 3. The main movement of the workpiece forming is driven by the first motor 1 through the first reducer 2 to rotate the hexagonal transmission shaft. Each group of sprocket chain pairs of the workpiece boxes 3 on both sides transmits the torque to the workpiece p...
Embodiment 2
[0054] The displacement of the tooling box 3 on both sides of the application is realized by the linkage screw 9, the second motor 7 is installed above the first motor 1, and the model of the second motor 7 is ECMA-C20807RS; the second reducer 8 is installed on The right end of the second motor 7, the model of the second reducer 8 is PLF80-10; the left side of the linkage screw 9 is connected to the output hole of the second reducer 8 and runs through the bottom of the tooling box 3 on both sides, The linkage screw 9 is arranged on the front side of the hexagonal transmission shaft, and the two do not affect each other; the displacement of the tooling box 3 is driven by the second motor 7 through the second reducer 8 to rotate the linkage screw 9, and is installed on both sides of the linkage screw 9 The tooling box body 3 begins to move toward each other, and the sprocket wheel 6 fixedly installed on the bottom of the tooling box body 3 follows the tooling box body 3 displacem...
Embodiment 3
[0056] The core-pulling positioning mechanism 11 of the present application penetrates through the middle of the tooling box body 3, and the left and right core-pulling positioning mechanisms 11 are on the same axis. The core-pulling positioning mechanism 11 includes: a core-pulling cylinder 10 , a core-pulling rod 12 , and a core-pulling tower head 14 . The core-pulling cylinder 10 is located at the tail end of the core-pulling positioning mechanism 11. The model of the core-pulling cylinder 10 is SC150X50. The front end of the core-pulling cylinder 10 is provided with a core-pulling rod 12, which is installed inside the tooling box 3 , The front end of the core-pulling rod 12 is provided with a core-pulling tower head 14, the core-pulling tower head is provided with 12 expansion flaps 19, and the outer ring of the core-pulling tower head is provided with a workpiece positioning account plate 13. The loading and unloading positioning of the workpiece generates relative motion...
PUM
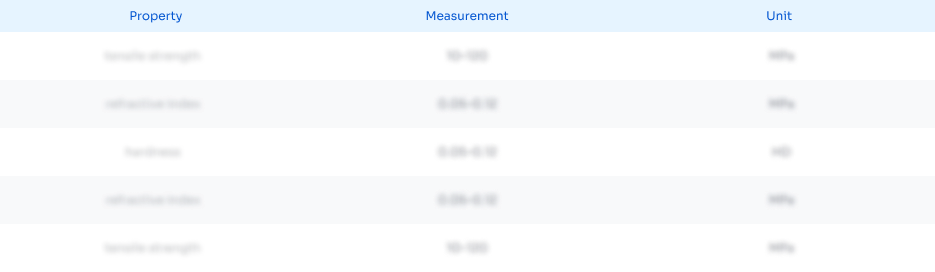
Abstract
Description
Claims
Application Information

- R&D Engineer
- R&D Manager
- IP Professional
- Industry Leading Data Capabilities
- Powerful AI technology
- Patent DNA Extraction
Browse by: Latest US Patents, China's latest patents, Technical Efficacy Thesaurus, Application Domain, Technology Topic, Popular Technical Reports.
© 2024 PatSnap. All rights reserved.Legal|Privacy policy|Modern Slavery Act Transparency Statement|Sitemap|About US| Contact US: help@patsnap.com